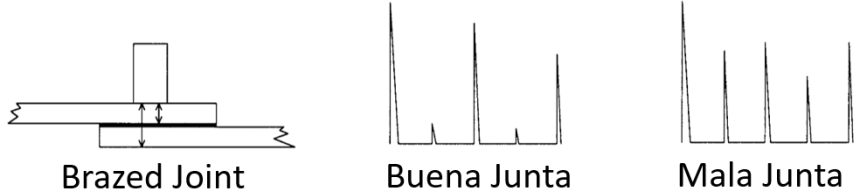
Un resumen de lo que se ve en nuestro curso de ultrasonido industrial nivel II, específicamente relacionado a la inspección de algunos tipos de componentes con equipos de defectología. El material a continuación se basa en el libro NDT Fundamentals de John Drury.
1. Inspección de piezas vaciadas con ultrasonido industrial
Algunas características de los componentes vaciados son las siguientes:
- Normalmente no se diseñan para aplicaciones críticas, es decir, sus aplicaciones no tienen requerimientos extremos, suelen estar bajo cargas de compresión.
- Debido a que sus aplicaciones no son críticas, la presencia de discontinuidades producto de la inherencia del material en la colada no “afectara” su desempeño.
- Algunos componentes vaciados si van a requerir de una inspección exhaustiva para poder desempeñar su aplicación de una manera correcta.
- Los métodos de inspección normalmente implementados son: líquidos penetrantes, radiografía industrial y ultrasonido industrial. LP se implementa para la superficie, mientras que RI y UT para evaluar el volumen.
- El método de ultrasonido industrial puede resultar difícil con algunas piezas vaciadas debido al ruido que puede ser generado por los granos de la pieza.
- Otro problema que puede presentarse con el método de ultrasonido industrial es en relación a las condiciones de la superficie del vaciado. Dependiendo de la calidad de superficie del vaciado la esta puede tener aspereza y generar problemas de acoplamiento.
Capacidad de inspección de un vaciado
El método de inspección seleccionado va a tener un gran impacto en la capacidad de reconocimiento, pero realmente lo que va a determinar la capacidad de inspección va a ser el vaciado en sí. El objeto inspeccionado establecerá las limitantes de la inspección y la selección del método de vaciado dictaminará las cualidades del objeto.
Comentarios respecto a la inspección ultrasónica
- Uno de los factores más importantes es la correcta selección de la frecuencia debido a la gran atenuación que pueden generar los granos presentes.
- La superficie es fundamental para que el haz ultrasónico ingrese de una manera adecuada. Si la superficie no tiene buenas características para la inspección ultrasónica se puede maquinar la zona a inspeccionar, pero recordando que eso no entraría dentro de la inspección. Sería un requerimiento para poder efectuar la inspección.
- Cuando se inspeccionan componentes vaciados es de suma importancia entender la metalurgia del componente para evitar caer en indicaciones falsas.
2. Inspección de piezas forjadas con ultrasonido industrial
Antes de hablar de los defectos que podemos encontrar en las piezas forjadas hay que recordar los defectos que se arrastran en los lingotes de fundición:
- Inclusiones no metálicas como Óxidos de Si y Al.
- Cavidades de reducción. Primarias y secundarias.
- Cuerpos extraños como piezas de herramientas o restos del horno de fundición.
- Segregación.
Estas indicaciones pueden aparecer en función de la calidad de los lingotes utilizados. Las piezas forjadas tienen una característica clave que les da la resistencia mecánica que poseen y además facilita la inspección ultrasónica.
Esta característica es la alineación de los granos en el material. Esto se debe a que las indicaciones prefieren colocarse en una dirección paralela a esta alineación y por lo tanto la inspección ultrasónica se deberá realizar perpendicular a las líneas de flujo.
Lo más recomendable para la inspección ultrasónica de piezas forjadas que son complejas es hacerlo de la siguiente manera:
3. Inspección exhaustiva con ultrasonido industrial
Una inspección de la pieza previo al forjado y posteriormente una inspección exhaustiva sobre la pieza terminada sobre todas las áreas que la pieza permita reconocer.
4. Inspección de laminaciones
La inspección de placas o tuberías que van a ser soldadas o maquinadas es una práctica muy común de ultrasonido industrial. Es una aplicación relativamente sencilla que se efectúa con haz longitudinal. Esta inspección puede generar problemas cuando se inspeccionan componentes delgados.
5. Procedimiento estándar
- Calibrar el sistema ultrasónico y dentro de los ajustes permitir que se observen dos ecos de la pared posterior.
- Colocar el transductor en la pieza a inspeccionar y ajustar los valores de ganancia para que el segundo eco tenga el 100% de la pantalla.
- Evaluar la pieza buscando por laminaciones que generalmente se encontrarán en la zona media de la pieza inspeccionada; esa indicación generara una reducción de la amplitud de la segunda indicación de la pared posterior. En algunos casos puede suceder que la reducción de la amplitud de la pared posterior se genere sin una indicación de laminación, se tiene que verificar que la reducción no sea producto de las condiciones superficiales o un mal acoplante.
6. Inspección de láminas delgadas
El problema de la medición de laminaciones ocurre cuando se estudian componentes muy delgados. El motivo del problema es que al ser delgado significa que las indicaciones generadas por la laminación y las indicaciones producto de la pared posterior estarán muy unidas y el equipo no tendrá la resolución suficiente como para discernir las señales. En caso de que se puedan discernir, quizás la confiabilidad no será la suficiente para garantizar los resultados.
Para realizar estas inspecciones podemos ejecutar una técnica llamada “técnica de múltiples ecos”.
7. Procedimiento de la técnica de múltiples ecos
- Colocar el transductor en una zona de la pieza evaluada que no posea laminaciones.
- Ajustar los parámetros del equipo para obtener múltiples señales de la pared posterior y que excedan por lo menos el 50% del eje horizontal de la pantalla. Observando así un comportamiento de caída de izquierda a derecha producto de la atenuación.
- Evaluar la pieza buscando laminaciones, la presencia de laminaciones hará que la señal tenga indicaciones más próximas entre sí y por lo tanto la señal se atenuara más rápido.
- . Estas pueden ser inspeccionadas mediante ultrasonido de haz recto, longitudinal. El principio de inspección es muy parecido, por no decir igual, que el implementado en la inspección de laminación.
8. Inspección de Brazed Joints
Si el espesor permite una clara distinción entre las reflexiones de pared podemos decir que la inspección de este tipo de juntas se puede ejecutar mediante el procedimiento implementado para la inspección de laminaciones.
Debido a que el material implementado para realizar la junta tendrá una impedancia acústica diferente a la de las paredes, se tendrá una indicación producto de esa interferencia de la superficie acústica. Esta técnica lo que buscará es un incremento de la señal de esa superficie.
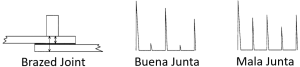
Ahora bien, cuando las paredes del material son muy delgadas y no permiten diferencia los ecos se tiene que recurrir a la técnica de los múltiples ecos, esta fue descrita en la inspección de laminaciones.
9. Inspección de Bonded Joints
Las juntas generadas por adherencia pueden ser juntas de metal a metal, así como, de metal a no-metal. La técnica implementada para ejecutar esta inspección es a través de la técnica de múltiples ecos. Cada vez que el pulso llega la interfaz entre los materiales adheridos una porción de la energía será transmitida al material adherido y absorbido.
En el caso de que el pulso llegue a una interfaz en donde no hay adherencia toda la energía será reflejada. Si evaluamos las señales de la técnica de múltiples ecos la diferencia entre ambos casos es evidente.
Los comentarios están cerrados.