- 1. Propiedades generales de las partículas magnéticas
- 2. Partículas Magnéticas Secas
- 3. Partículas Magnéticas Húmedas
- 4. Selección del tipo de partícula. Húmeda o Seca.
Partículas Magnéticas
Las partículas magnéticas son el componente que le permitirá al inspector detectar las discontinuidades ya que sin la presencia de las partículas no se podrá visualizar la presencia de la fuga de flujo y en consecuencia la presencia de discontinuidades.
Las partículas se pueden aplicar de dos maneras al componente, de manera seca o húmeda. Cada una de estas tendrá sus ventajas y limitaciones.
De manera muy simplificada podemos decir que las partículas secas se aplican en forma de polvo sobre la superficie del componente y las partículas húmedas se mezclan con un medio líquido que posteriormente es aplicado a la superficie del material.
Por otra parte también tenemos que pensar que las partículas magnéticas pueden ser visibles bajo iluminación normal o bajo iluminación fluorescente, siendo entonces partículas fluorescentes o partículas visibles.
1. Propiedades generales de las partículas magnéticas
Para obtener los mejores resultados del método las características propias de la partícula magnética serán un factor determinante ya que la correcta selección de las partículas es crucial para la confiabilidad de la generación de las discontinuidades.
Si las partículas implementadas no tienen las propiedades correctas se pueden caer en errores en los resultados debido a una pobre generación de las discontinuidades o simplemente incapacidad de poder generarlas.
Dentro del método de partículas magnéticas existen dos tipos de partículas que pueden ser implementadas: partículas secas y partículas húmedas.
Las partículas secas son aquellas que se aplican directamente sobre el componente sin la necesidad de tener un medio liquido (las partículas en suspensión).
Las partículas húmedas son aquellas que se encuentran en suspensión en un medio líquido, el cual puede ser base agua o base oleosa.
Otro punto importante a mencionar con respecto a las partículas implementadas en el método, es que estas pueden ser visibles bajo condiciones de iluminación natural o fluorescente bajo condiciones de iluminación de luz ultravioleta. Esta característica correspondiente a la visibilidad gira en torno a un pigmento que se le coloca a las particulas como recubrimiento.
Ahora bien, de manera general y sin realizar ningún tipo de discriminación con respecto al tipo de partícula podemos mencionar algunas características deseables:
Alta permeabilidad: Se busca la mayor permeabilidad posible ya que esto le permitirá a la partícula magnetizarse fácilmente y por lo tanto detectar rápidamente las fugas de flujo. Ahora bien, alta permeabilidad no significa alta sensibilidad ya que hay otros factores a tomar en cuenta como geometría, si la partícula es húmeda o seca, entre otras propiedades.
Baja retentividad: Se debe buscar una baja retentividad ya que esto le permitirá a las partículas que sean removidas de la superficie de la pieza fácilmente. Si la retentividad fuera alta significaría que además de magnetizarse fácilmente por la alta permeabilidad mantendrían dicha magnetización, lo cual genera un problema de visibilidad de las indicaciones reales por la gran cantidad de partículas (se disminuye el contraste y enmascara las discontinuidades reales).
Tamaño de la partícula: El tamaño es variable y afectara los resultados pero dependerá del tipo de partícula: seca o húmeda.
Geometría de la partícula: La geometría que posea la partícula magnética afectara directamente la movilidad y el poder de atracción que esta tenga. De manera general podemos hablar de dos geometrías.
- Partículas esféricas: Este tipo de partículas brindara una excelente movilidad pero tendrán bajo poder de atracción.
- Partículas alongadas: Este tipo de partículas brindara un excelente poder de atracción pero tendrán una baja movilidad.
Movilidad: La movilidad en la superficie de la pieza es un factor importante para maximizar la detección ya que baja movilidad significa una reducción en la detectabilidad.
Pigmentación: Las partículas magnéticas tienen un pigmento en su capa para brindarle contraste en la aplicación y por lo tanto detectabilidad. Dicho pigmento puede o no ser fluorescente.
Material: Es un poco evidente pero igual lo mencionamos, el material de las partículas magnéticas debe ser un material magnético, con alta permeabilidad y baja retentividad.
2. Partículas Magnéticas Secas
Las partículas magnéticas secas son aquellas que su no implementan un medio líquido para su aplicación. Se aplican en forma de nube de polvo o esparciéndolas sobre la superficie de la pieza evaluada.
Este tipo de partículas lo podemos encontrar en distintas presentaciones y colores. Los colores típicos serian: rojo, gris, amarillo y negro. Pero el factor determinante en la selección adecuada del color será el contraste que genere con la pieza a inspeccionar. En la siguiente figura podemos apreciar algunos ejemplos.
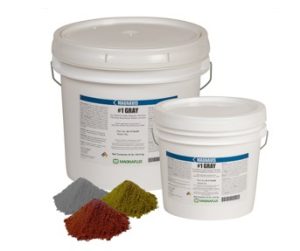
Tal y como se observa en la figura anterior las partículas como tal son suministradas en forma de polvo dentro de recipientes.
Un punto importante a mencionar es que las partículas secas son no fluorescentes a diferencia de las partículas húmedas que pueden ser no fluorescentes y fluorescentes.
2.1 Efecto del tamaño en las partículas secas
Para entender el impacto que tiene la correcta selección del tamaño de las partículas pensemos en el efecto que tiene partículas finas y gruesas.
Partículas Finas: En las partículas secas se consideran partículas pequeñas aquellas que tienen un tamaño de 50mm. Estas partículas serán mucho más livianas que las partículas grandes y por lo tanto tendrán una mayor sensibilidad para la detección de discontinuidades pequeñas producto de su movilidad. Las partículas finas acarrean un problema por su naturaleza de polvillo: se esparcen fácilmente con la brisa, se adhieren fácilmente a contaminación en la superficie y quedan atrapadas.
Partículas Gruesas: La presencia de partículas gruesas es necesaria en la formulación de las partículas debido a que las partículas gruesas controlan la naturaleza de polvo que tienen las partículas finas, es decir facilitara su manipulación. Además de que en el caso de discontinuidades grandes la presencia de partículas gruesas jugara un rol fundamental para fungir como una especie de puente que permita mantenerse en la superficie en vez de caer dentro de la discontinuidad.
Tamaño de las partículas magnéticas secas: Al evaluar el efecto que tienen las partículas finas y gruesas podemos decir que una correcta formulación referente al tamaño es una mezcla entre partículas finas y gruesas. Ciertamente será el fabricante quien se encarga de esta formulación pero es importante que los inspectores tengan este conocimiento.
2.2 Efecto de la geometría en las partículas secas
La geometría de la pieza, al igual que el tamaño también tiene influencia en los resultados del ensayo, especialmente en el efecto que tiene la geometría en la correcta aplicación de las partículas secas.
Recordemos que este tipo de partículas se aplica mediante una nube de polvo o esparcimiento a lo largo de la superficie, esto quiere decir que las partículas flotaran en el aire y posteriormente caerán sobre la superficie. Para entender el impacto que tiene la geometría en este fenómeno evaluemos la siguiente geometría.
Partículas alongadas: Este tipo de partículas tiene la capacidad de alinearse muy bien a las líneas del campo magnético, por lo tanto son deseables para la sensibilidad. Ahora bien, este geometría acarrea un problemática la cual es que las partículas se aglutinaran entre si y traerán problemas a la hora de la aplicación.
Partículas esféricas: La presencia de partículas esféricas en la formulación de las partículas secas resultara en partículas con buenas características de aplicación.
Geometría de las partículas magnéticas secas: Al evaluar el efecto que tienen las partículas alongadas y esféricas podemos decir que una correcta formulación referente a la geometría es una mezcla entre ambas. Ciertamente será el fabricante quien se encarga de esta formulación pero es importante que los inspectores tengan este conocimiento. Ahora bien, de manera general podemos mencionar que se suele tener una relación entre 1:1 y 2:1.
2.3 Movilidad de las partículas secas y aplicación
Cuando apliquemos las partículas secas se busca aplicarlas desde una distancia adecuada que permita que las partículas caigan lentamente sobre la superficie. Esto debido a que si las partículas se lanzan bruscamente sobre la superficie se puede tapar indicaciones débiles. En la siguiente figura se aprecia una bomba para la aplicación de las partículas secas.
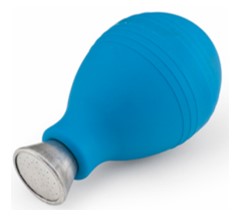
Un punto importante tiene que ver con la geometría de la pieza que se va a inspeccionar. En el caso de que la superficie de “recepción” de las partículas sea horizontal facilita el hecho de como las partículas se asientan directamente y no tendrán movilidad una vez caigan en la superficie. Ahora bien, se les puede brindar una leve movilidad al vibrar el componente o con la implementación de corriente alterna.
2.4 Comentarios generales
Las partículas magnéticas secas no pueden ser reutilizadas debido a que se disminuirá la sensibilidad en su aplicación ya que las partículas finas tienen una alta probabilidad de “perderse” y no ser recolectadas para una nueva aplicación. Es por ello que esta práctica, además de ser poco práctica, no es viable.
Cuando se utilicen partículas magnéticas secas es sumamente importante garantizar que no tienen una magnetización residual dentro de la botella, esto debido a que puede causar que se acumulen y resulta difícil su aplicación.
Una manera fácil de desmagnetizar las partículas secas es con un yugo electromagnético con AC. Colocarlos alrededor de las partículas y poco a poco alejar el yugo, esto disminuirá sustancialmente la magnetización residual.
3. Partículas Magnéticas Húmedas
Las partículas magnéticas húmedas a diferencia de las partículas secas se encuentran en suspensión en un medio líquido, ya sea base agua o base oleosa.
Desde un punto visto técnico la ventaja que brinda que el penetrante sea húmedo es que hay un aumento sustancial de la sensibilidad ya que la movilidad de las partículas aumenta y permite que las partículas finas sean utilizadas en mayor porcentaje en comparación a las partículas secas. Esto producto a las perdidas por adherencia y esparcimiento asociadas a las partículas secas.
Otra gran ventaja que brinda el método húmedo es que la aplicación de las partículas es uniforme a lo largo de la superficie de la pieza evaluada lo cual beneficia los resultados de la prueba.
Otro gran diferenciador que tienen las partículas húmedas es la posibilidad de implementar partículas fluorescentes y no fluorescentes. El factor que determina la fluorescencia es el pigmento que se implementa para recubrir la partícula. En la siguiente figura podemos apreciar un caso de partículas visibles y partículas fluorescentes.
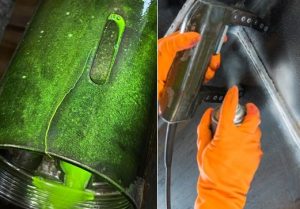
Tal y como se aprecia en la figura anterior ambos casos logran detectar con claridad la discontinuidad pero la técnica fluorescente brinda una ventaja evidente con respecto a la sensibilidad. La fluorescencia le facilita al técnico inspector realizar una inspección visual mucho más efectiva además de brindar mayor sensibilidad para detectar discontinuidades pequeñas.
Ahora bien, la implementación de la técnica fluorescente requiere de instrumentación adicional para activar la fluorescencia en las partículas, la cual se logra mediante la aplicación de luz ultravioleta.
3.1 Medio liquido de la suspensión
Existen dos tipos de medios implementados para ser implementados como vehículos para las partículas magnéticas, estos son:
- Agua
- Aceite
A continuación presentamos una tabla con algunas de las diferencias entre estos medios.
Agua | Aceite |
---|---|
Requiere inhibidores de corrosión | No genera corrosión en el material inspeccionado |
Puede ser un riesgo para conexiones eléctricas | No tiene este efecto |
Susceptible a generar corrosión intergranular en algunos componentes | No tiene este efecto |
Tiene bajo costos en comparación a las partículas base aceite | Son más costosos |
No presenta riesgos de incendio | Presenta riesgos de incendio |
Poca limpieza posterior a la inspección | Requiere de mayor limpieza posterior a la inspección |
Requieren de agentes para mejorar la mojabilidad | No requiere de agentes para mejorar la mojabilidad. Ya que tienen muy buena mojabilidad |
La presencia de los agentes para la mojabilidad genera un problema de generación de espuma. La espuma se acumula en la parte superior de la mezcla y en la aplicación puede borrar las indicaciones. Es por ello que se necesita agregar agentes que hagan que la espuma sea inestable para que desaparezca rápidamente | No hay generación de espuma |
Las partículas húmedas base agua tienen la limitante con respecto a temperaturas bajo cero ya que el medio se congelara impidiendo el desarrollo de la prueba. Ahora bien, el congelamiento no es instantáneo y por lo tanto la prueba si se podría desempañar bajo ciertas condiciones. En el caso de temperaturas muy bajas se deberá utilizar anticongelante aunque esto disminuye la sensibilidad | Las partículas húmedas base oleosa con respecto a temperaturas bajas tendrán la limitante de la viscosidad del medio |
Dependiendo del tipo de medio implementado la viscosidad puede variar. El mantenimiento de este baño de partículas magnéticas es sumamente importante para garantizar buenos resultados. Esto debido a la presencia de contaminantes, variación de la concentración y cualquier otra eventualidad | El mantenimiento de este baño de partículas magnéticas es mucho menor en comparación a uno base agua. La concentración de partículas se mantiene mucho más constante |
3.2 Efecto del tamaño de las partículas húmedas
El tamaño típico de estas partículas es de alrededor de 10mm y menos. En el caso de partículas sintéticas de óxido de hierro podemos estar hablando de tamaño de diámetro de alrededor de 0,1mm.
El motivo por el cual estas partículas son más pequeñas que las implementadas para la técnica seca se debe a dos razones. La primera seria debido a mientras más pequeña la partícula más sensibilidad. En segundo lugar y el motivo práctico es que si las partículas son muy grandes es difícil mantenerlas en suspensión en su medio.
3.3 Efecto de la geometría en las partículas húmedas
El impacto que tiene la geometría de las partículas no es tan importante como en el caso de las partículas secas.
Esto se debe a que debido a que las partículas se encuentran suspendidas en un medio y dicho líquido dictara el movimiento y flujo de las partículas. Ahora bien, debido a que el medio liquido es mucho más denso que el aire el movimiento como tal será mucho más lento y por lo tanto tendrán mucha más capacidad de acumularse de una manera más confiable en las discontinuidades.
Por lo tanto, no es necesario tener geometrías específicas para favorecer o no la implementación de las partículas.
3.4 Movilidad de las partículas húmedas
Por el hecho de que las partículas se encuentran en un medio líquido podemos decir que la movilidad en comparación al método seco es mucho mayor.
Si pensamos en la movilidad al aplicar las partículas sobre una superficie estas podrán moverse en un plano bidimensional en la superficie. En el caso de la aplicación mediante inmersión las partículas tendrán un campo de movilidad tridimensional.
Es sumamente importante que las partículas puedan moverse adecuadamente y abarcar toda la superficie del componente para asentarse correctamente y poder generar resultados adecuados.
3.5 Aplicación de partículas húmedas
Las partículas húmedas son aplicadas de distintas maneras, pero para entender esto debemos pensar en las distintas presentaciones comerciales en las que las podemos conseguir. Algunas de estas se presentan en la siguiente figura.
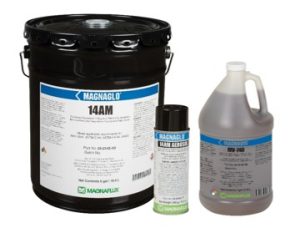
Tal y como se observa en la figura anterior las partículas húmedas las podemos encontrar en latas tipo aerosol, bidones y recipientes.
Con respecto a cómo podemos aplicar las partículas magnéticas es prudente dividir su aplicación en dos grupos.
- Aplicaciones con sistemas portátiles
- Aplicaciones en equipo estacionario
3.5.1 Aplicación de partículas húmedas en sistemas portátiles
En el caso de aplicaciones en sitio la manera típica para implementar las partículas húmedas es mediante rociado.
Ahora bien, dicho rociado se puede conseguir a través de diversas técnicas. Algunas de estas son:
Lata de aerosol: La vía más común para aplicar las partículas magnéticas en campo. En este caso la formulación de las partículas en el medio viene directamente del fabricante y no se debe elaborar ninguna consideración a excepción de la fecha de vencimiento.
Pistolas presurizadas: La implementación de sistemas de rociado para la aplicación de partículas magnéticas también es viable. Siendo esta técnica menos portátil ya que requiere que la pistola se encuentre conectada a una fuente de partículas húmedas. Dichas partículas deben ser preparadas previamente.
3.5.2 Aplicación de partículas húmedas en sistemas estacionarios
Más adelante se cubrirán los sistemas de inspección estacionarios pero para fines de este apartado debemos mencionar que estos sistemas son equipos que permiten la magnetización e inspección de componentes de una manera rápida y eficiente. Teniendo como principal desventaja la movilidad y las dimensiones de las piezas que puede inspeccionar.
En la siguiente figura se aprecia un banco de partículas magnéticas.
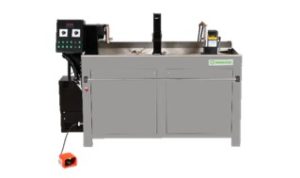
La figura anterior muestra un banco horizontal. Para este tipo de sistemas se debe tener un reservorio de la formulación de las partículas húmedas, el cual debe ser cuidadosamente preparado y mantenido, esto se verá más adelante.
Si pensamos en como aplicamos las partículas húmedas en estos sistemas tenemos dos alternativas, las cuales son:
Inmersión: Esta técnica se aplica en componentes con alta retentividad ya que es necesario que la técnica sea de magnetización residual. Esto debido a que en primer lugar se magnetiza la pieza y luego se introduce en el baño de partículas magnéticas las cuales son agitadas gentilmente para garantizar homogeneidad de las partículas y minimizar los errores de los resultados por movimiento de las partículas producto de la agitación. El tiempo de inmersión es proporcional significa más tiempo de exposición a las partículas y por lo tanto una mejora en los resultados, lo cual es una ventaja sobre la técnica residual por manguera.
Aplicación por manguera: En esta técnica se aplican las partículas mediante una manguera que genera un flujo de las partículas húmedas sobre la superficie de la pieza evaluada. En este caso la técnica de magnetización es continua. Por lo tanto, cuando las partículas ya se encuentran en la superficie del componente el suministro de la manguera se apaga y se inicia la magnetización del componente y posteriormente se procede a la evaluación de las indicaciones.
3.6 Formulación, concentración y contaminantes en el baño de partículas húmedas
Las partículas magnéticas húmedas pueden ser preparadas previamente por el fabricante o pueden ser elaboradas mediante la adquisición de las partículas en condición seca para luego ser mezcladas con el medio líquido.
A excepción del caso de las partículas húmedas que vienen en presentación de lata de aerosol es sumamente importante el mantenimiento ya que la confiabilidad que brindaran en la inspección estará ligada a su correcta formulación, concentración y carencia de agentes contaminantes.
3.6.1 Formulación de las partículas húmedas
La formulación del concentrado de las partículas magnéticas se debe realizar en función de las recomendaciones del fabricante para poder obtener los mejores resultados bajo el diseño del sistema. En la siguiente figura podemos apreciar un concentrado de partículas magnéticas para ser mezcladas con agua.
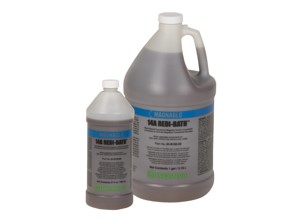
En la figura anterior se aprecia un producto de partículas magnéticas diseñado para ser mezclado con agua para generar el baño de partículas magnéticas. En este caso este producto, por recomendación del fabricante se deberá mezclar según las recomendaciones del fabricante que se encuentran en la hoja de especificaciones del componente, en este caso particular se aprecia en la siguiente figura.
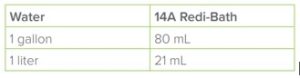
Como podemos apreciar se implementan apenas 21mL del concentrado en un Litro de agua para obtener la formulación adecuada según el fabricante.
Por otra parte podemos evaluar otro producto que se proporciona en forma seca para ser mezclado posteriormente, este se presenta a continuación.
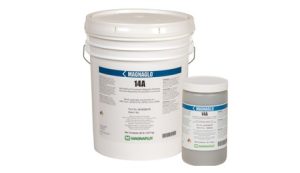
En este caso este producto se encuentra en condición de polvo, y se puede mezclar tanto con agua como con una base de aceite.
En el caso de agua se deben seguir las recomendaciones del fabricante, las cuales incluyen: añadir agentes para mejorar la mojabilidad, añadir agentes para disminuir la formación de espuma, añadir las partículas secas, revolver por tiempos determinados. Evidentemente el correcto cumplimiento de los pasos para la formulación del componente determinara su eficacia.
Por otro lado este mismo polvo se puede mezclar con una base oleosa e igualmente se deberá seguir las recomendaciones del fabricante para generar la formulación. En este caso, simplemente se deberá mezclar las partículas secas con la cantidad necesaria del medio según el fabricante. A continuación se presenta una figura con algunas presentaciones comerciales de la base oleosa.
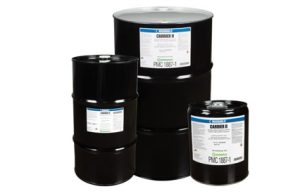
Tal y como se aprecia en la figura anterior las presentaciones de la base oleosa satisfacen diversos requerimientos.
3.6.1.1 Preparación de la mezcla
Los sistemas estacionarios o recipientes para producir la mezcla pueden ser sistemas que tengan un sistema de recirculación del producto o no.
En el caso de que el reservorio tenga un sistema de recirculación el trabajo de generar la mezcla será mucho más fácil, en caso contrario el trabajo deberá ser manual y puede ser susceptible a una distribución desigual a lo largo de su medio.
Para los sistemas que tienen recirculación el sistema tiene una bomba que permite que el fluido este en constante agitación, garantizando el mezclado y homogeneidad.
3.6.2 Concentración de las partículas húmedas
Es evidente que las partículas magnéticas se encuentran en un medio ya sea de base agua o aceite. Pero es muy importante tomar en cuenta la cantidad de partículas magnéticas que habrá en un determinado volumen del vehículo, es decir una concentración.
La concentración es sumamente importante ya que la correcta cantidad de partículas determinara los resultados de la inspección, la falta de partículas disminuirá la sensibilidad y el exceso producirá enmascaramiento de discontinuidades.
Para determinar la concentración de partículas visibles se implementan las pruebas AMS3042 y AMS3043. Para la concentración de partículas fluorescente se implementan las pruebas AMS3044 y AMS3045. Si pensamos en la prueba ASTM aplicable seria la ASMT E-1444.
Para efectuar esta prueba se implementa un tubo de vidrio en forma de pera, tal y como se aprecia en la siguiente figura.
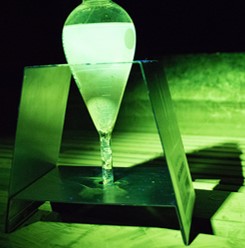
Se recomienda leer la norma ASTM E1444, específicamente el punto 7.2.1.1. A groso modo establecemos algunos pasos para el caso de partículas fluorescentes:
- Agitar la suspensión por lo menos 30minutos para garantizar la distribución uniforme de las partículas en el medio.
- Colocar 100mL de la muestra en el tubo designado para la evaluación. En donde tenga incrementos de 0,05mL para partículas fluorescente y 0,1mL para visible.
- Desmagnetizar la muestra y colocar en reposo por 60minutos.
- Leer el volumen de partículas presente en la muestra.
- Evaluar en función de las tolerancias permisibles dentro del procedimiento. En caso de ser partículas fluorescentes se deberán evaluar bajo luz ultravioleta.
- Si las partículas no se ven solidas sino como una especie de aglomerado de partículas se deberá repetir la prueba. En caso de que la segunda prueba obtenga el mismo resultado se deberá cambiar toda la suspensión.
4. Selección del tipo de partícula. Húmeda o Seca.
Para el caso de la selección de partículas húmedas o secas podemos mencionar algunas directrices generales en función de los siguientes puntos:
- Tipo de Discontinuidad: Para discontinuidades subsuperficiales las partículas secas suelen ser más sensibles. Esto se debe a la alta permeabilidad y el hecho de ser partículas alongadas. Al implementar partículas secas con corriente alterna brinda buenos resultados para discontinuidades superficiales pero cuando el requerimiento incluye grietas superficiales finas el método húmedo es mucho mejor independientemente de la corriente de magnetización.
- Tamaño de la Discontinuidad: Las partículas húmedas suelen brindar mejores resultados para discontinuidades poco profundas que sean finas o anchas.
- Conveniencia: La aplicabilidad de las partículas húmedas o secas también dependerá del factor de portabilidad que ofrezca el método. Especialmente de la herramienta de magnetización y si esto lo asociamos a el beneficio que brindara el tipo de corriente al tipo de partícula se termina extendiendo al tipo de partícula.
En el caso de la selección de partículas fluorescentes o visibles radica sobretodo en la conveniencia de aplicación y la disponibilidad de los equipos necesario. De manera general podemos decir que el método húmedo visible y el método húmedo fluorescente tienen prácticamente la misma sensibilidad. Aunque si es importante recalcar que bajo de ciertas condiciones de iluminación el fluorescente es más fácil de detectar.