- Capítulo 6: Equipos, técnicas y requerimientos de magnetización
- 1. Sistemas Portátiles
- 2. Equipos semiportátiles
- 3. Equipos Estacionarios
- 4. Técnica Continua y Residual
- 5. Requerimientos y cálculos para la magnetización
Capítulo 6: Equipos, técnicas y requerimientos de magnetización
Los equipos implementados para la magnetización en el método de partículas magnéticas básicamente los podemos dividir en dos grupos: portátiles y estacionarios.
Es fácil de entender que la aplicación dictaminara el tipo de equipo que debemos o estaríamos limitados a utilizar. Suponiendo que debemos hacer una inspección en campo traviesa de un cordón de soldadura deberíamos asumir que el equipo adecuado para la aplicación sería uno portátil ya que un equipo estacionario no solamente sería difícil de llevar, sino que además la fuente de corriente no estaría disponible.
Por otra parte, si lo que estamos buscando en productividad de trabajo para piezas que pueden ser manipuladas fácilmente probablemente un sistema estacionario puede resultar sumamente beneficioso.
Sistemas Portátiles
Yugo Electromagnético – Inducción Indirecta – Campo Longitudinal
La magnetización con Yugo Electromagnético es una de las más implementadas en situaciones en donde predomina la movilidad por parte del sistema de inspección y las condiciones del componente permiten la evaluación mediante el yugo.
En la siguiente imagen podemos apreciar un yugo electromagnético.
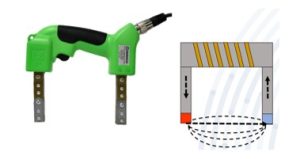
En la imagen presentada se aprecia un yugo electromagnético, se observa que consta de dos patas metálicas que entran en contacto con la superficie evaluada. Por otra parte cuenta con un cuerpo en el cual se tiene una bobina tal y como se aprecia en el croquis de la figura.
La magnetización mediante el yugo es del tipo indirecta ya que la corriente fluye es a través de la bobina que generara el campo magnético que será inducido en la pieza. De manera adicional el campo inducido en la pieza será del tipo longitudinal.
Yugo de Imán Permanente – Inducción Indirecta
Los yugos de imán permanente como bien lo dice su nombre logran la magnetización del componente debido a la presencia de un imán permanente. El yugo de imán permanente se observa en la siguiente figura.
En la figura anterior podemos observar dos yugos electromagnéticos, simplemente observando la imagen podemos apreciar el gran beneficio que brinda trabajar con un imán permanente, siendo este la carencia de una fuente eléctrica. Esto permite que el yugo de imán permanente tenga una portabilidad superior a las otras técnicas.
La magnetización que brinda este tipo de yugo es longitudinal.
Bobinas portátiles – Inducción Indirecta
Otro sistema portátil seria la implementación de bobinas diseñadas con la portabilidad en mente. En la siguiente figura podemos apreciar una bobina.
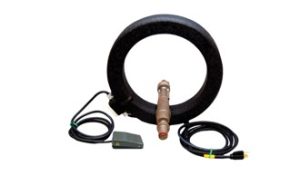
En la figura anterior podemos apreciar una bobina, se observa como la bobina tiene un punto de conexión que permite implementarla con una fuente de corriente comercial por lo tanto no requiere de una fuente semiportatil o estacionaria.
Las bobinas pueden variar en diámetro para la magnetización de diversos tipos de piezas.
La magnetización que genera la bobina es del tipo indirecta y longitudinal.
Equipos semiportatiles
Este tipo de equipos son básicamente fuentes de generación que a pesar de ser relativamente grandes y robustas tienen la capacidad de movilizarse a los componentes que requieran inspección. En la siguiente imagen podemos observar algunos sistemas semiportatiles de partículas magnéticas.
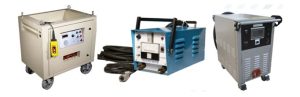
Como podemos observar en la imagen anterior estos equipos son sustancialmente más grandes que un yugo electromagnético pero siguen teniendo la capacidad de ser trasportado al sitio de implementación.
Estos equipos móviles tienen la capacidad de generar altos valores de corriente que facilitan la inspección de componentes grandes.
El voltaje con el que estos tipos de equipo operan varía dependiendo de la marca y modelo pero usualmente trabajan con un voltaje de 220V.
Con respecto a la corriente que pueden generar también varía dependiendo de la marca y modelo pero podemos agrupar a groso modo en dos rangos de corriente generada. Equipos móviles de bajo rango generan una corriente entre 500A y 1500A. También existen equipos móviles con un mayor poder de generación, aquí estaríamos hablando de una corriente entre 3000A y 6000A.
Estos tipos de equipos normalmente generan dos tipos de corriente: Corriente Alterna y HWAC.
Ahora bien, los equipos que se observaron en la imagen anterior solamente fungen como el generador de la corriente para la magnetización pero necesitan una herramienta para transmitir la corriente al componente ya sea de manera directa o indirecta. Podemos hablar de dos tipos de aplicaciones:
- Magnetización con Electrodos.
- Magnetización con Cables.
Electrodos – Inducción Directa – Campo Circular
Los electrodos son una herramienta que permiten introducir una corriente eléctrica en un componente, usualmente son de cobre debido a su alta conductividad. En la siguiente figura podemos apreciar una magnetización con el uso de electrodos.
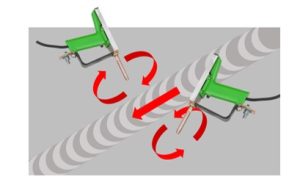
Tal y como se aprecia en la figura anterior la corriente fluye a través de los electrodos, sabiendo que la corriente fluye a lo largo del electrodo y sabiendo que el campo magnético es perpendicular a dicho recorrido obtendremos un campo magnético circular en función de los electrodos.
La magnetización con los electrodos resulta sumamente útil cuando el tamaño del componente limita la aplicación de otras técnicas y se desea obtener una magnetización circular.
Normalmente se implementa DC o HWAC, en ambos casos el amperaje requerido para la magnetización será el mismo. Sin embargo, el tipo de corriente HWAC consume mucho menos voltaje y por lo tanto los efectos de temperatura producida en los puntos de contacto del electrodo se ven disminuidos. De manera adicional el HWAC también produce una mayor movilidad de las partículas que la corriente DC.
Cables
Los cables son sumamente útiles para ciertas aplicaciones ya que brindan el beneficio de la flexibilidad en su uso.
Se pueden implementar para hacer pasar el flujo de corriente a través del componente o también se pueden enrollar alrededor del componente para inducir indirectamente el campo magnético.
A continuación se muestra una imagen de un equipo con cables para la magnetización.
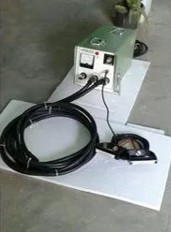
La longitud de los cables varía en función de la aplicación pero se puede hablar de un rango de 4m a 30m. Es importante recordar que a medida que el cable es más largo la fuerza de la magnetización disminuye, es por ello que para algunas aplicaciones se recomiendan cables cortos.
Equipos Estacionarios
Los equipos estacionarios son equipos que no tienen la posibilidad de desplazarse debido a su tamaño y condiciones de operación.
Por lo tanto, los componentes a ser inspeccionados con este sistema de inspección deben poderse trasladar y además de cumplir unas dimensiones máximas de tamaño para poder ser inspeccionado mediante alguna de las técnicas que ofrece el sistema estacionario.
Estos equipos estacionarios tienen la capacidad de generar una magnetización lineal y circular en el componente mediante: bobinas, contacto directo o conductor central.
Este tipo de equipo suele ser un equipo estacionario que no es adaptable a trabajo en campo. Puede generar magnetización lineal y circular. En la siguiente figura podemos apreciar cómo se logran dichas magnetizaciones.
El sistema estacionario más común es el banco horizontal húmedo. En la siguiente figura se aprecia uno de estos equipos.
Tal y como se aprecia en la figura anterior, el banco horizontal posee una bobina movible y puntos de contacto movibles para adaptarse a la configuración del componente a evaluar.
Dependiendo de la marca y modelo del equipo los tipos de corriente varían al igual que los rangos de corriente que puede implementar. Pero de manera general podemos mencionar que pueden trabajar con AC, DC, HWDC y FWDC. Con respecto al amperaje de la corriente podríamos estar hablando de valores entre 2500A hasta los 10000A.
Un punto importante a mencionar es que para la aplicación de las partículas húmedas se debe desconectar la fuerza magnetización justo antes de empezar el flujo del líquido, esto para eliminar cualquier riesgo de chispas o arco eléctrico.
Magnetización mediante el uso de bobinas – Inducción Indirecta – Campo Longitudinal
Sabemos que la implementación de una bobina generara un campo longitudinal en el componente mediante una inducción indirecta. En la siguiente figura se observa un ejemplo de un componente siendo magnetizado por una bobina en un equipo estacionario.
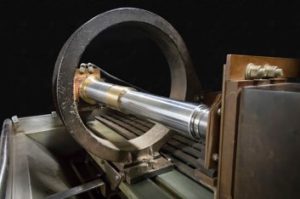
En la figura anterior observamos como la bobina alrededor de la pieza.
Magnetización mediante Head Shot – Inducción Directa – Campo Circular
El equipo estacionario también puede generar una magnetización circular en el componente mediante dos contactos con los cuales se sujeta la pieza, a través de dichos contactos se introduce un flujo de corriente en la pieza. Esta técnica de magnetización en el equipo estacionario se suele llamar en inglés como “Head Shot”. En la siguiente figura podemos apreciar esta técnica de magnetización.
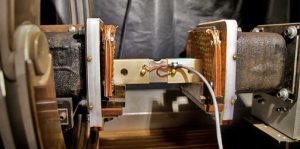
Tal y como se observa en la figura anterior la pieza se encuentra sujetada por contactos de cobre que están conectados a la fuente de corriente del equipo estacionario. Estos contactores se pueden ajustar en función del tamaño de la pieza evaluada.
Magnetización mediante el uso de un conductor central – Inducción Indirecta – Campo Circular
Otra técnica que puede ser implementada con el equipo estacionario es la magnetización mediante el uso de un conductor central. Esta técnica se puede implementar cuando el componente a evaluar tiene una zona hueca que permite pasar un tubo de cobre a través de este orificio. Esto se puede apreciar en la siguiente figura.
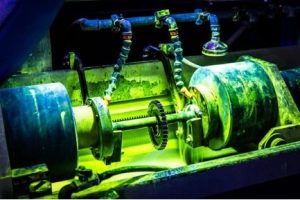
Tal y como se observa en la imagen, se tiene un componente que eta siendo magnetizado circularmente mediante una inducción indirecta.
Técnica Continua y Residual
Como ya se ha mencionado anteriormente la presencia de un campo magnético que genere la fuga de flujo por las discontinuidades es crucial para el método.
Tal y como se observó en la curva de histéresis sabemos que la retentividad del campo magnético varía dependiendo del tipo de material.
Si pensamos en la evaluación del componente podríamos realizarlo de dos formas.
Forma Continua
Esta técnica se basa en que la aplicación de las partículas magnéticas se realiza al mismo tiempo que la aplicación de la fuerza de magnetización.
La forma continua suele ser la técnica predilecta cuando se requiere obtener la máxima sensibilidad.
Esto es fácil de entender ya que al tener la fuerza de magnetización constante siempre se llegara a los picos de voltaje de cada uno de los tipos de corriente, independientemente del tiempo (Esto no aplica para corriente directa y FWAC).
Por otra parte la fuerza del campo magnético no sufrirá una disminución como puede ocurrir al remover la fuente de magnetización. Recordemos que al eliminar la fuente de magnetización la curva de histéresis llevara el comportamiento del material al punto de retentividad y dependiendo del material este puede que no brinde la sensibilidad mínima para la prueba. Supongamos un material con alta permeabilidad, será difícil de magnetizar y además su retentividad será baja.
Otra ventaja que provee el método continuo es que dependiendo del tipo de corriente implementado brindara una movilidad adicional a las partículas magnéticas en la superficie del componente evaluado, esto aplica para el caso de corriente alterna o corriente pulsada.
Forma Residual
La forma residual quiere decir que antes de aplicar las partículas magnéticas se magnetiza el componente y se retira la fuente de magnetización y solamente se trabaja con el campo magnético residual que permita las propiedades magnéticas del componente.
No suele ser un método aplicado normalmente, pero si puede resultar sumamente efectivo para materiales con alta retentividad. En dicho caso esta técnica puede ahorrar mucho tiempo debido a la automaticidad que se le puede brindar
Requerimientos y cálculos para la magnetización
La cantidad de corriente que se debe implementar para magnetizar el componente para la prueba de partículas magnéticas variara dependiendo de múltiples factores como la geometría de la pieza, conductividad del material, tipo de corriente, técnica de magnetización, entre otras variables.
La correcta selección del nivel de la corriente es fundamental ya que tener la cantidad apropiada brinda los resultados adecuados. De esto podemos decir lo siguiente:
- Si se excede por encima la cantidad de corriente necesaria puede resultar en una acumulación excesiva de partículas magnéticas y se pueden enmascarar indicaciones.
- Otro fenómeno que puede ocurrir al excederse de la cantidad necesaria de corriente es que la pieza evaluada puede sufrir una quemadura puntual.
- Si el nivel de la corriente es inferior al necesario puede que no se genere suficiente fuga de flujo magnético y en consecuencia no se atraerán las partículas para denotar las indicaciones.
Ahora bien, ¿Cuál es el amperaje que tenemos que implementar?
La manera más fácil de responder esta pregunta es simplemente diciendo: Siguiendo lo establecido en el procedimiento.
Entonces para ello nos vamos a basar en la norma ASTM E1444/E1444M – 12, titulada: Práctica estándar para prueba con partículas magnéticas.
Amperaje para la magnetización circular directa
Si leemos el punto X3.3 de la ASTM E1444 podremos ver las especificaciones para este tipo de magnetización.
A manera de repaso recordemos que magnetización directa significa que la corriente pasa a través del componente evaluado y magnetización circular quiere decir que se tendrá un campo con recorrido circular en la pieza evaluada.
La norma establece que se deberá implementar un rango de corriente entre 300A y 800A por pulgada de diámetro del componente. Ahora bien, el diámetro lo definimos como la distancia más grande entre dos puntos en la circunferencia externa del componente-
Si pensamos en una barra que tiene un diámetro de tres pulgadas podríamos establecer de manera general que el amperaje debería ser entre 900A y 2400A.
En el caso de componentes con geometrías relativamente complejas hay que definir correctamente el procedimiento de inspección. Un ejemplo puede ser la siguiente pieza:
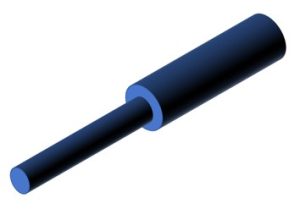
Tal y como se aprecia el componente tiene dos secciones cada una con un diámetro diferente, esto quiere decir que el cálculo del amperaje será diferente para cada sección.
Por lo tanto, para realizar la inspección mediante partículas magnéticas correctamente tenemos que pensar en realizar la inspección por etapas.
Suponiendo que la sección delgada tiene 1″ de diámetro y la sección gruesa tiene 2″ de diámetro tendremos que los rango de amperaje serán: 300A y 800A para la sección delgada y 600A y 1600A para la sección gruesa.
Una recomendación para la magnetización de componentes con múltiples secciones es siempre inspeccionar las zonas con menor amperaje primero ya que si se magnetiza con el mayor amperaje se deberá desmagnetizar para luego magnetizar, este paso se elimina si se realiza en un orden ascendente.
Amperaje para la magnetización circular indirecta mediante conductor central
Si leemos el punto X3.4 de la ASTM E1444 podremos ver las especificaciones para este tipo de magnetización.
En este caso sabemos que se pasa una corriente a través de una barra central que se coloca dentro del componente a evaluar.
El cálculo de la corriente es muy similar al presentado en el punto 6.1 pero hay que hacer dos acotaciones. La primera seria la correcta interpretación del diámetro de la pieza y en segundo lugar, la ubicación del conductor central en referencia al componente.
En el caso de que la inspección solamente quiera tomar en cuenta la superficie interna de la pieza el diámetro a considerar será: la distancia más grande entre dos puntos internos que se encuentren a 180˚ entre sí. Por el contrario, si se desea inspeccionar el componente en su totalidad el diámetro se obtiene como se mencionó en 6.1.
Otra variable a mencionar es la ubicación del conductor central en referencia a la pieza evaluada. Y realmente deberíamos pensar en dos casos, tal y como se aprecia en la siguiente figura.

En la figura anterior observamos dos casos de magnetización con conductor central.
Magnetización con el conductor central en el eje central
En este caso la magnetización el conductor central se ubica en lo que sería el eje central de la pieza evaluada. La corriente se calcula igual que en el caso 6.1, es decir: un rango entre 300A y 800A por pulgada de diámetro del componente.
Magnetización con el conductor central en contacto con superficie interna
En este caso la magnetización el conductor central se ubica contacto con la superficie interna. Tal y como se aprecia en la figura el radio de acción de la magnetización se ve disminuida ya que la fuerza de magnetización no parte desde el centro geométrico. Dicho de radio de acción es equivalente a un radio de cuatro veces el diámetro del conductor central, aproximadamente. Para poder inspeccionar la totalidad del componente hay que rotar la pieza.
Con respecto a la corriente que se debe aplicar para este caso también equivale al presentado en 6.1, es decir: un rango entre 300A y 800A por pulgada de diámetro del componente.
Pero, la consideración del diámetro varía en este caso. El diámetro en este caso es igual al diámetro del conductor central más el doble del espesor de la pieza inspeccionada.
Amperaje para la magnetización lineal mediante el uso de bobinas
Al implementar una bobina para la generación de magnetización lineal en el componente hay que tener una consideración muy importante incluso antes de seleccionar el amperaje de la corriente.
La primera consideración es seleccionar que tamaño de bobina se va a implementar. En la siguiente figura podemos observar algunos tipos de bobinas.
Tal y como se aprecia en la figura anterior podemos implementar varios tamaños y esto repercute en cómo se da la magnetización en el componente. Pero al igual que el tamaño de la bobina puede cambiar también puede cambiar el tamaño del componente evaluado.
Por lo tanto, aquí más bien deberíamos de hablar de un factor de llenado de la pieza evaluada en función del área transversal de la bobina. En la siguiente figura apreciamos el cambio con respecto al factor de llenado.
Tal y como se aprecia en la figura anterior tenemos cuatro bobinas que van desde los 2,5″ hasta los 1,25″ y en cada caso se evalúa el factor de llenado con respecto a una pieza que tiene 1″ de diámetro.
Ahora bien, en cada caso el factor de llenado varia y esto tiene un impacto directo en cómo se debe calcular la cantidad de corriente a suministrarle a la bobina para generar la magnetización.
Otro factor sumamente importante es referente a la longitud del componente a evaluar, en la siguiente figura observamos la diferencia.
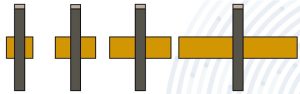
Tal y como se aprecia en la figura anterior observamos como de izquierda a derecha aumenta el tamaño del componente a evaluar. Según la ASTM E1444 la distancia efectiva de magnetización de la bobina se extiende en ambas direcciones de la bobina por una distancia de aproximadamente del radio de la bobina. Ahora bien, es importante utilizar los medidores de gauss para garantizar la magnetización.
Si la longitud del componente no permite que la inspección se pueda realizar en un solo disparo se deberá realizar lo permitido para abarcar toda la longitud, un ejemplo se aprecia en la siguiente figura.
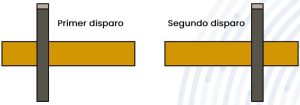
Tal y como se aprecia en la figura anterior para inspeccionar este componente se realizan dos disparos. Es importante en el proceso de posicionar el objeto que se deje un traslape de al menos 10% de la longitud del componente para garantizar que la inspección de todo el componente.
Ahora bien, luego de todas estas consideraciones que se han mencionado con respecto a las bobinas podemos introducir los cálculos asociados a la determinación de la corriente a implementar. Pero estos cálculos se segmentan en función del factor de llenado en cuatro grupos:
- Bobinas con bajo factor de llenado.
- Bobinas con facto de llenado intermedio.
- Bobinas con alto factor de llenado o mediante cables.
- Magnetización con bobinas en piezas huecas.
Antes de ver cada uno de estos grupos es valido mencionar que el resultado de estos cálculos brindara un valor de corriente que debe ser utilizado como referencia, posteriormente se deberan utilizar las herramientas de verificacion para garantizar buenos resultados.
Por otra parte, es sumamente importante tomar en cuenta que las formulas que se presentaran en los proximos puntos solamente seran validas si se cumplen las siguientes condiciones:
- La relacion entre la longitud y diametro de la pieza evaluada, es decir L/D, es mayor que 2 y menor que 15.
- En caso de que L/D sea menor que 2 se deberan añadir piezas ferromagneticas del mismo diametro del componente evaluado en ambos extremos de la pieza para compensar la longitud.
Bobinas con bajo factor de llenado
Un bajo factor de llenado significa que el área transversal de la bobina es igual a 10 veces o más el área transversal de la pieza evaluada.
En el caso de que la pieza no se ubique en el centro sino en contacto con la superficie interna de la bobina se implementa la formula a continuación.
NI=K/(L/D)(±10%)
En donde,
N= El número de vueltas de la bobina.
I= El amperaje aplicado a la bobina.
K= Constante de permeabilidad, igual a 45000.
L= Longitud de la pieza evaluada.
D= Diámetro de la pieza evaluada.
En caso de que la pieza evaluada se ubique en el centro de la bobina se implementa la siguiente formula:
NI=KR/((6L/D)-5)(±10%)
En donde,
N= El número de vueltas de la bobina.
I= El amperaje aplicado a la bobina.
K= Constante de permeabilidad, igual a 43000A.
R= Radio de la bobina en pulgadas.
L= Longitud de la pieza evaluada.
D= Diámetro de la pieza evaluada.
Bobinas con factor de llenado intermedio
Un factor de llenado intermedio significa que el área transversal de la bobina es entre 2 y 10 veces el área transversal de la pieza evaluada. En este caso se implementa la siguiente formula.
NI=〖(NI)〗_h [(10-“τ” )/8]+〖(NI)〗_l [(“τ” -“2” )/8]
En donde,
N= El número de vueltas de la bobina.
I= El amperaje aplicado a la bobina.
〖(NI)〗_h= El valor de NI calculado para bobinas de alto factor de llenado.
〖(NI)〗_l= El valor de NI calculado para bobinas de bajo factor de llenado.
“τ” = La relación entre áreas transversales de la bobina y pieza evaluada. Es decir= (π〖r_bobina〗^2)/(π〖r_pieza〗^2 )
Bobinas con alto factor de llenado o cables
Un factor de llenado alto significa que el área transversal de la bobina es menos de 2 veces el área transversal de la pieza evaluada. Para este caso también podemos asumir que la bobina puede ser realizada mediante cable embobinado alrededor de la pieza, debido a que este arreglo también generara un alto factor de llenado. En este caso se implementa la siguiente formula.
NI=K/((L/D+2))(±10%)
En donde,
N= El número de vueltas de la bobina.
I= El amperaje aplicado a la bobina.
K= Constante de permeabilidad, igual a 43000A.
L= Longitud de la pieza evaluada.
D= Diámetro de la pieza evaluada.
Piezas huecas y su relación L/D
Componentes huecos o parcialmente huecos
En el caso de los componentes que son huecos o parcialmente huecos el valor del diámetro “D” se deberá reemplazar por un diámetro efectivo Deff. El cálculo de este valor se realiza mediante la siguiente formula:
D_eff=2〖((A_t-A_h)/π)〗^(1/2)
Donde,
At= El área transversal total de la pieza evaluada.
Ah= El área transversal de la sección hueca.
Componentes cilíndricos huecos
En el caso de los componentes que son huecos o parcialmente huecos el valor del diámetro
D_eff=〖(〖(OD)〗^2-〖(ID)〗^2)〗^(1/2)
Donde,
OD= Diámetro externo del cilindro.
ID= Diámetro interno del cilindro.
Amperaje cuando se implementan electrodos
El amperaje implementando electrodos varía en función del espesor pero otro factor importante a tomar en cuenta es el distanciamiento entre los electrodos, para ello podemos ver la siguiente tabla.
Espesor del Material | Distanciamiento entre electrodos | Amperajes |
---|---|---|
¾in o menos | 3.5 a 4.5 A/mm | 90 a 115 A/in. |
¾in o más | 4.0 a 5.0 A/mm | 100 a 125 A/in. |
El espaciado entre los electrodos nunca debe ser menos a 2″ o mayor a 8″.
La zona efectiva de magnetización es un cuarto del distanciamiento entre los electrodos, hacia cada lado de la línea recta que conecta a los electrodos.z