Los equipos de ultrasonido al igual que la mayoría de los equipos del área de ensayos no destructivos se basan en comparaciones.
Decir que se basan en comparaciones es decir que utilizan referencias conocidas para poder evaluar objetos desconocidos. Para poder decirle al equipo cual es esa referencia conocida se utilizan los patrones de referencia.
Por lo tanto, el proceso de calibración del equipo no es solo es recomendada, sino que es necesaria para el funcionamiento adecuado del equipo. Los equipos de inspección se diseñan para una aplicación específica y se le debe decir al equipo que está viendo mediante la calibración para que sea capaz de interpretar los datos y generar resultados.
Si revisamos la práctica recomendada SNT-TC-1A, tenemos dos definiciones que nos pueden apoyar para esta explicación.
- Calibración, Instrumento: La comparación de un instrumento con una referencia, normalmente trazable al Instituto Nacional de Estándares del país aceptable.
- Estandarización, Instrumento: el ajuste de un instrumento de NDT usando una referencia apropiada para obtener o establecer una respuesta conocida y reproducible. (Normalmente se ejecuta previo a la examinación, pero puede ser efectuada en cualquier momento que se tenga duda en la respuesta del equipo).
1. Tipos de Equipos de Ultrasonido
Existe una gran variedad de equipos de ultrasonido en el mercado y evidentemente los tipos de equipo los podríamos categorizar por las técnicas de inspección que realizan. Pero de manera general dividiremos los tipos de equipos en tres grupos. Los cuales son:
- Medidores de Espesores: Estos equipos son diseñados para la medición rápida de espesores. Una de sus aplicaciones principales es para líneas de producción en donde se desea saber si la pieza pasa o no una condición conocida. Este tipo de equipos basan su presentación de resultados en una representación numérica y en caso de que tengan una imagen Tipo-A esta sería secundaria.
Debido a la forma de la presentación de los resultados este tipo de equipos son excelentes para aplicaciones puntuales en donde se sabe exactamente lo que se está viendo. No son equipos destinados para dimensionamiento de fallas.
En la siguiente figura podemos ver algunos ejemplos de medidores de espesores.

- Detectores de Fallas: Los equipos de detección de fallas son equipos que se utilizan para la evaluación de la integridad interna de los productos. La representación de los resultados se basa en una imagen Tipo-A que permite evaluar más detenidamente una falla. Con este tipo de representaciones se pueden buscar grietas, fallas, delaminaciones, entre otras discontinuidades.
Este tipo de equipos se utilizan cuando la pieza a evaluar tiene defectos que pueden tener varias naturalezas y varios orígenes. Por lo tanto, se puede estimar que se va a encontrar, pero realmente no se sabe que hay hasta que se evalúa y es por ello que se necesita un equipo de detección de fallas. En la siguiente figura podemos ver algunos ejemplos de detectores de fallas.
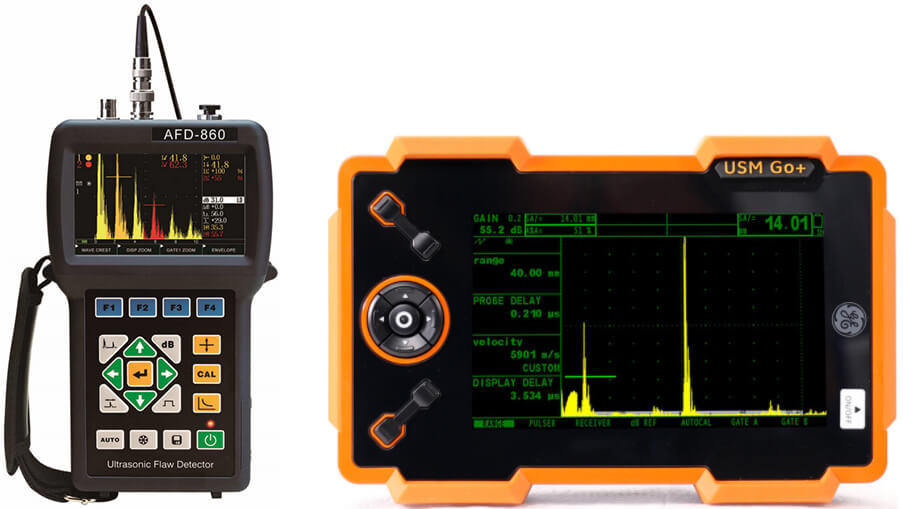
- Equipos de Defectología Avanzados: Este tipo de equipos al igual que los detectores de fallas basan su evaluación en imágenes Tipo-A. La diferencia que tienen es que implementan algoritmos de evaluación para obtener resultados mediante técnicas ultrasónicas un poco más avanzadas que una imagen Tipo-A convencional.
Algunas de las técnicas que podríamos agrupar en este tipo de equipos serian: Arreglo de Fase (PAUT), Difracción de Tiempo de Vuelo (TOFD) y el Método de Focalización Total (TFM).
En la siguiente figura podemos ver algunos ejemplos de equipos de Defectología Avanzados.
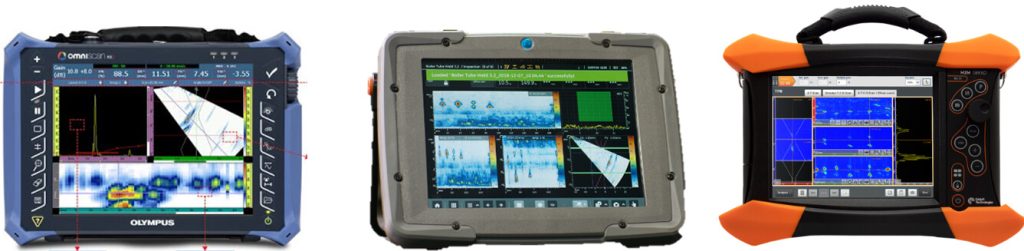
2. Tipos de Imágenes en Ultrasonido
Hoy en día es muy sencillo entender el concepto de pantalla, solamente hay que observar un “smartphone”. Toda la información que podemos ver en el celular en representada por la pantalla de este dispositivo y exactamente lo mismo ocurre en los equipos de ultrasonido, la pantalla es la interfaz que permite al inspector observar/analizar/evaluar los resultados de la inspección.
La pantalla es indiscutiblemente el medio que permite el análisis de la información, pero antes de hablar de los tipos de pantallas que existen observemos la siguiente figura.
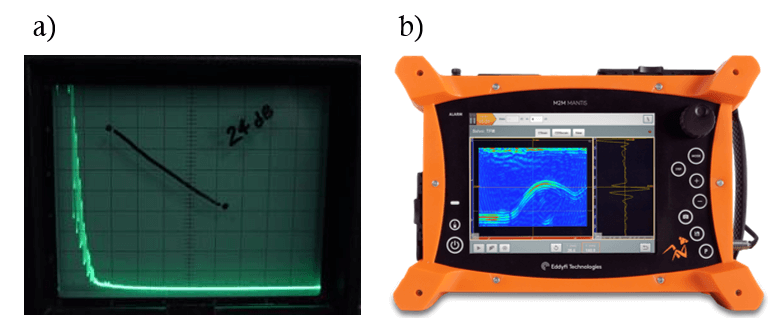
En la Figura 2.6.1 podemos observar la diferencia entre los primeros equipos de inspección ultrasónica con los más modernos. La diferencia evidentemente es radical y esto se debe a los avances de la tecnología.
Debido a la calidad de las imágenes que podemos tener hoy en día es necesario hablar acerca de los pixeles y la resolución.
Los pixeles son cada una de los cuadrados que genera la pantalla y cada uno de estos pixeles toma un color y el conjunto de todos los pixeles de la pantalla genera la imagen como tal. En la siguiente figura podemos ver la representación de una cuadricula de pixeles.
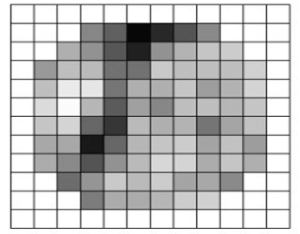
En la Figura 3.6.2 vemos múltiples cuadrados en la cuadricula, cada cuadrado es un pixel. Ahora bien, la cantidad de pixeles que tenga nuestro equipo de inspección determinará la calidad de la imagen que podrá representar y esto se puede explicar fácilmente mediante la siguiente figura.

En la Figura 2.6.3 apreciamos como de izquierda a derecha la cantidad de pixeles va incrementado, en la primera de la izquierda tenemos 1 pixel, luego 4, luego 25 y así sucesivamente hasta llegar a 10000 pixeles.
Al aumentar la cantidad de pixeles mejoramos drásticamente la resolución y vemos como en la imagen de 100×100 pixeles vemos de manera nítida la letra R. Aquí se observa la importancia de los pixeles y la resolución de los equipos de inspección.
Las pantallas digitales y los procesadores implementados hoy en día nos permiten generar imágenes con la información producida por los ecos de la inspección.
Estas imágenes van a permitirle al inspector evaluar la información de distintas maneras, que dependiendo de la aplicación beneficiara o no.
La selección adecuada de la imagen será determinante para poder producir un buen análisis de los resultados.
Los tipos de imágenes más comunes son:
- Imagen Tipo A
- Imagen Tipo B
- Imagen Tipo C
2.1 Imagen Tipo A
La imagen tipo A-Scan es la más básica que se puede tener en ultrasonido, el resto de las representaciones se generan a partir del A-Scan. Este tipo de imagen permite conocer la distancia a la que se encuentra la discontinuidad y la amplitud de la onda. En la Figura 2.1 se aprecia dicha representación.
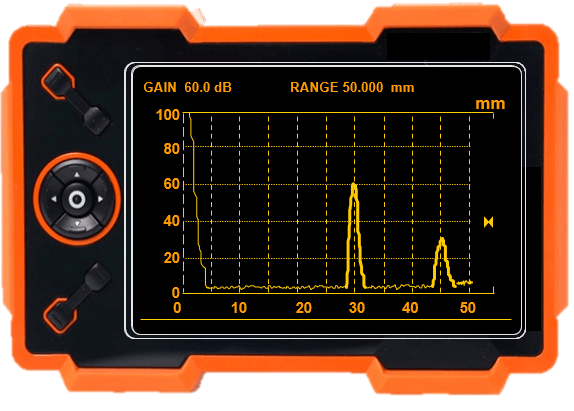
De la figura anterior podemos mencionar que el eje vertical representa la amplitud de la onda y el eje horizontal el tiempo. El pulso generado por la onda ultrasónica está representado por la línea amarilla.
2.2 Imagen Tipo B
En segundo lugar, se tiene la representación tipo B-Scan la cual provee una visión de la pieza a lo largo de uno de sus ejes.
Esta imagen se obtiene mediante un conglomerado de imágenes Tipo A. El equipo procesa la información y genera esta nueva imagen. La manera para obtener múltiples imágenes tipo A para ser procesada es moviendo el transductor a lo largo de un eje, posteriormente el equipo procesa la información y se obtiene una imagen como la presentada en la siguiente figura.

Si detallamos en la Figura 2.2 en la Imagen Tipo B podemos decir que el eje vertical representa el espesor de la pieza y por lo tanto la profundidad de la discontinuidad mientras que el eje horizontal será la longitud de la pieza (o el recorrido de la inspección).
Ahora bien, si queremos evaluar la amplitud de cada una de las señales debemos pensar que eso se aprecia en la Imagen Tipo A pero la visualización de la amplitud en la Imagen Tipo B se aprecia por la paleta de colores, el color nos dará un valor de amplitud.
2.3 Imagen Tipo C
Tal y como observamos que la imagen Tipo B se genera a partir de una unificación de imágenes tipo A tenemos que decir que ocurre lo mismo con la imagen Tipo C. La diferencia es que en este caso no ocurre solamente en un eje, sino que se requieren dos ejes.
Por lo tanto, podemos decir que el tipo de visualización C-Scan muestra la pieza en dos dimensiones.
Para sistemas de inspección que deseen obtener este tipo de imagen se requiere de un encoder que permita mover el transductor a las coordenadas requeridas para poder producir este tipo de imagen. En la Figura 2.3.1 se visualiza esta representación.
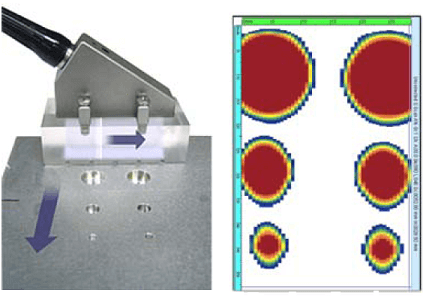
Podemos decir de la Figura 2.3.1 que observamos una vista aérea de la pieza inspeccionada, en donde podemos apreciar la imagen en dos dimensiones. Por otra parte, y al igual que la imagen tipo B, la amplitud la evaluamos por la paleta de colores de la imagen.
3. Transductores
Los transductores son una pieza clave en el sistema de inspección de ultrasonido. Este componente genera las vibraciones mecánicas utilizadas para introducir el ultrasonido en el componente evaluado. Existen diferentes tipos de transductores, pero el más utilizado es el transductor electromecánico que funciona bajo el fenómeno piezoeléctrico (En este manual no se contemplan otros tipos).
El diseño del transductor dependerá de las especificaciones del fabricante y la selección se basará, entre otros factores, en la aplicación. De manera general, existen 4 tipos de transductores:
- Haz recto de contacto.
- Haz angular de contacto.
- Doble cristal de contacto.
- De inmersión.
A continuación, se presenta un ensamble típico de un transductor de haz recto:
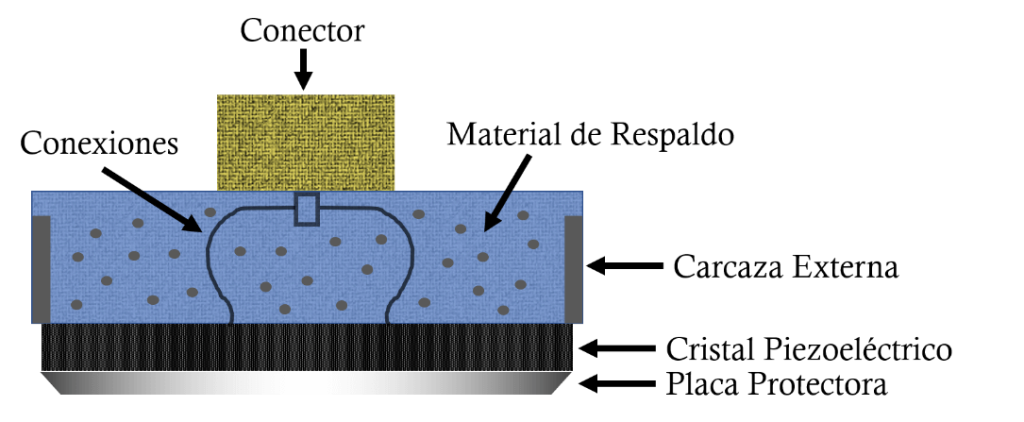
Cada una de las piezas señaladas en la Figura 3.1 posee un efecto determinante en el funcionamiento del transductor. Es por ello que a continuación se explicara cada uno de ellos en detalle.
3.1 Transductores de Haz Recto
En la siguiente figura se muestra un ejemplo de un transductor de haz recto.

Este tipo de transductores poseen un único cristal piezoeléctrico con el que generan la onda ultrasónica. Normalmente están destinados para la generación de ondas longitudinales y por lo tanto para aplicaciones que utilicen este tipo de onda.
Algunas de las aplicaciones comúnmente conocidas que implementan ondas longitudinales son la detección de defectos laminares y medición de espesores.
3.2 Transductores de Haz Recto con Línea de Retardo
A los transductores de Haz Recto se le puede colocar una línea de retardo. En la siguiente figura se muestra un ejemplo.
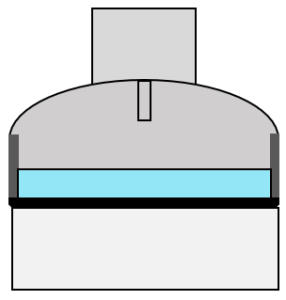
La línea de retardo es un componente plástico (plexiglás) que se acopla al transductor y puede ser muy útil para ciertas aplicaciones.
Su nombre línea de retardo se debe a que básicamente lo que producirá en la inspección es un retardo en el tiempo de ingreso de la onda ultrasónica al material. Esto mejorara la inspección en la zona cercana a la superficie del material y también mejorara la medición de espesores de materiales delgados.
Las mejoras anteriores en relación al uso de la línea de retardo se deben a que ese retardo producirá que el campo cercano presente en el material se vea reducido y aparezca mas bien en la línea de retardo.
Ahora bien, para hacerlo de una manera mas puntual colocaremos algunas de las ventajas de implementar un transductor con línea de retardo:
- Proporciona buena resolución cercana.
- Cuando la línea de retardo tiene un contorno adecuado a la superficie mejora el acoplamiento en superficies curvas.
- Proporciona protección al transductor aumentando su tiempo de vida útil.
- Mejora las capacidades de inspección sobre materiales con temperaturas elevadas.
3.3 Transductores de Haz Angular
Estos transductores poseen un único cristal piezoeléctrico con el que generan la onda ultrasónica. La diferencia con los transductores de haz recto es que estos utilizan una zapata, normalmente de plástico (plexiglás), para la generación de ondas transversales.
La onda transversal se genera por la refracción con la zapata, generando una onda ultrasónica que ingresa al material con un ángulo establecido.
Las zapatas tienen múltiples diseños y ángulos, pero si hablamos de las zapatas estándar podríamos decir que los ángulos de refracción que poseen son de 30, 45, 60 y 70 grados.
De manera general podemos establecer una lista de las aplicaciones de transductores de haz angular:
- Inspección de uniones soldadas.
- Detección y dimensionamiento de grietas.
- Inspección de sistemas de tuberías, tubos, forjas, fundiciones y componentes estructurales.
En la siguiente figura podemos apreciar un ejemplo de transductores de haz angular.

En la figura anterior apreciamos que el transductor como tal puede estar integrado a la zapata o puede ser removible. En el caso de que sea removible tiene una ventaja debido a que la zapata en si establece el ángulo de refracción y por lo tanto podremos tener distintos ángulos al utilizar diferentes zapatas.
Otro punto importante de tomar en cuenta en los transductores angulares es que hay varios parámetros que afectaran la inspección. De una manera general podemos decir que son dos:
- El punto de salida del haz ultrasónico.
- El ángulo de refracción.
Estos dos puntos se supone que son fijos en las zapatas per es importante tomar en cuenta el desgaste que la superficie de la zapata puede tener con el constante roce con la superficie de inspección.
Es por ello que la verificación del punto de salida y del ángulo de refracción debe ser constantemente revisada para asegurar que los resultados de la inspección con transductor angular sean correctos.
3.4 Transductores duales
Los transductores duales tienen la característica de que poseen dos cristales piezoeléctricos. Uno para transmitir la onda y otro para recibirla.
Estos transductores logran la medición debido a que el haz ultrasónico realiza un recorrido en forma de V. La presencia de ese recorrido en forma de V mejora sustancialmente la medición de espesores en superficies con corrosión o superficies ásperas.
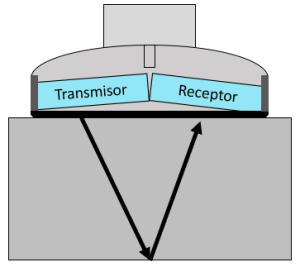
Como se aprecia en la figura anterior el recorrido sonoro claramente tiene un recorrido en forma de V. A continuación, se listarán algunas de las aplicaciones más comunes para los transductores duales.
Aplicaciones
- Medición del espesor remanente de pared.
- Monitoreo de corrosión.
- Inspección de soldadura de recubrimiento y determinar la adherencia.
- Detección de discontinuidades, inclusive en espesores delgados.
Al igual que las aplicaciones también se listarán las ventajas de los transductores duales.
Ventajas
- Con los transductores duales se elimina el disparo principal, mejorando la resolución cercana.
- El diseño de haz en V proporciona un pseudo foco, que hace más sensible la inspección de formas irregulares como corrosión o picaduras.
- Buen acoplamiento sobre superficies rugosas.
- Reduce el ruido en materiales de grano grueso o que tienen alta dispersión.
Ahora bien, debido a la forma con la que el haz ultrasónico viaja cuando se implementan transductores duales se genera una limitante bastante importante e imprescindible de conocer. Esta limitante es el hecho de que los transductores duales tendrán un rango de espesores para los cuales podrá ser utilizado, tendrá un espesor mínimo y uno máximo.
Esto se puede explicar mejor haciendo base en la siguiente figura.
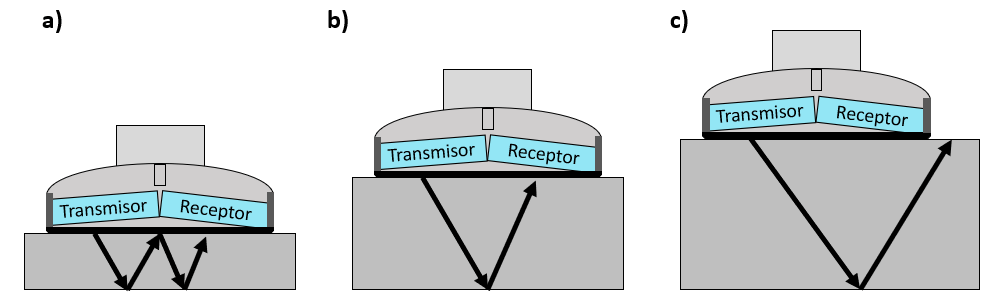
Lo que se busca con los transductores duales es que el recorrido sonoro sea como en la parte b de la figura 3.6.3.2. Cuando ocurre esto significa que la medición hizo el recorrido en V y los resultados serán correctos. Pero, ¿qué pasa si el espesor está por encima o por debajo de los permisibles? Lo que va a suceder es que vamos a tener errores e incluso malas interpretaciones de los resultados.
3.5 Transductores de inmersión
Estos transductores están diseñados para la inspección de piezas que se encuentras sumergidas parcial o totalmente. Debido a la condición de inmersión estos transductores tienen la capacidad de resistir inmersión sin comprometer los componentes internos. En la siguiente figura se muestra un ejemplo de un transductor de inmersión.

Estos transductores son comúnmente utilizados para sistemas automatizados de inspección. A continuación, se listan algunas de las aplicaciones de estos transductores.
Aplicaciones
- Barridos automatizados.
- Medición de espesores en línea.
- Detección de fallas a alta velocidad en tubería, barras, tubos, placas y otros componentes.
- Pruebas de transmisión.
- Aplicación de la técnica de tiempo de vuelo.
Por otra parte, podemos establecer algunas ventajas.
Ventajas
- Acoplamiento uniforme que reduce las variaciones de sensibilidad.
- Reducción del tiempo de barrido gracias a la automatización.
- Uso de transductores focalizado, que incrementan la resolución y la sensibilidad.
Otra de las características que se tienen que mencionar de los transductores de inmersión es que pueden tenerse de tres formas diferentes.
- No focalizados.
- Focalizados Esféricos.
- Focalizados Cilíndricos.
En la siguiente figura se puede apreciar el efecto de la focalización en el transductor de inmersión.
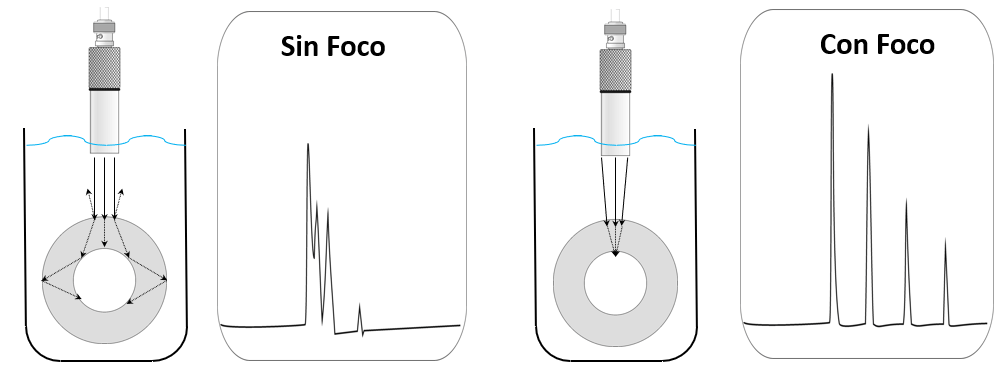
La focalización va a depender del radio de curvatura que se le dé la lente del transductor. Podríamos pensar que los lentes acústicos implementados en los transductores de inmersión comparten el diseño con los lentes utilizados para la vista.
3.6 Selección del Transductor
La selección del transductor para el sistema de inspección es una tarea del Nivel III encargado en desarrollar el procedimiento de inspección. Esto se debe a que dependiendo de las características de la inspección ciertos transductores tendrán ventajas y limitaciones con respecto a la inspección.
Algunos de los factores que podemos decir que se deberían tomar en cuenta a la hora de seleccionar el transductor son los siguientes puntos
- Tipo de defecto y material a inspeccionar.
- Profundidad del defecto.
- Criterios de aceptación requeridos.
- Condiciones ambientales.
Estos son algunos de los factores que pueden ser tomados en cuenta, pero también podemos utilizar las siguientes preguntas para esclarecer un poco el panorama.
¿Qué estoy inspeccionando?
Esta pregunta me dará el material y el tipo de material está fuertemente ligado al poder de penetración que debe tener mi sistema.
¿Qué estoy buscando?
Aquí se buscaría responder el tipo de discontinuidad que voy a encontrar. Esto me indicara que nivel de sensibilidad o resolución debería tener en primera instancia para poder encontrar dicha indicación. Ligándolo un poco con la profundidad que podría tener.
¿Cuál es mi criterio de aceptación?
Nuevamente hablamos de la sensibilidad y de la resolución que debe tener mi sistema de inspección.
Evidentemente la selección del transductor impactara directamente los resultados de la inspección y la selección debe ser correcta para ofrecer los mejores resultados. Si nos centramos en la selección de la frecuencia podemos establecer los siguientes puntos:
Transductor con Frecuencia Baja
- Estas penetran fácilmente a través del material debido a que se presenta menos atenuación.
- Se utilizan al inspeccionar piezas con granos gruesos o de superficies rugosas ya que se minimiza la perdida por dispersión.
- El ángulo de divergencia del haz es grande por lo que dificulta la evaluación de defectos pequeños.
Transductor con Frecuencia Alta
- Emiten un haz de mayor concentración con un mejor poder de resolución.
- Mayor dispersión del haz por efecto de estructuras de granos gruesos.
De aquí podemos extraer que solamente la selección de la frecuencia impactara en otros factores ya conocidos como la sensibilidad, resolución y penetración. De manera didáctica aquí se presenta una lista de relaciones entre diversas variables del sistema de ultrasonido.
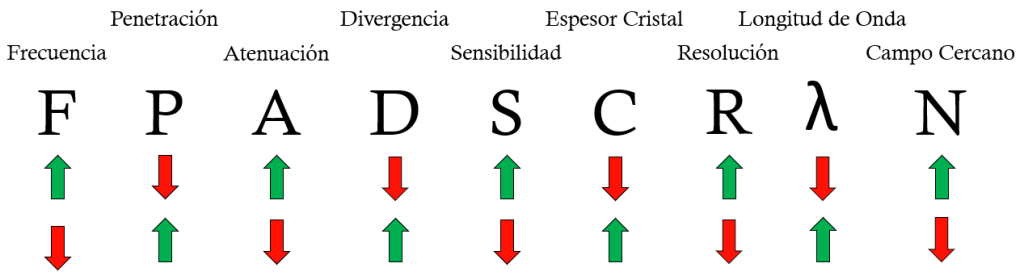
Un ejercicio sencillo basándonos en la figura anterior. Si queremos reducir el campo cercano de nuestra inspección deberíamos escoger un transductor con frecuencia baja. Esto también nos generará un aumento de la penetración, pero reducirá tanto la sensibilidad como la resolución.
Entonces aquí podemos volver a las preguntas. ¿Satisfago los requerimientos de sensibilidad y de resolución? Evidentemente el proceso de selección no es tan sencillo, pero para eso están los procedimientos y los bloques de calibración para garantizar que nuestras inspecciones sean confiables.
4. Cables y conexiones
Los cables y conexiones pueden pasar desapercibidas debido a que solamente son cables de conexión, pero sin estos cables no se puede efectuar ninguna inspección debido a que son cruciales para que el transductor y el equipo de inspección de comuniquen.
Hoy en día existen múltiples tipos de conexiones que pueden ser implementadas y evidentemente cada una tendrá sus ventajas y desventajas. Aquí solamente mostraremos algunas de ellas haciendo uso de la siguiente figura.
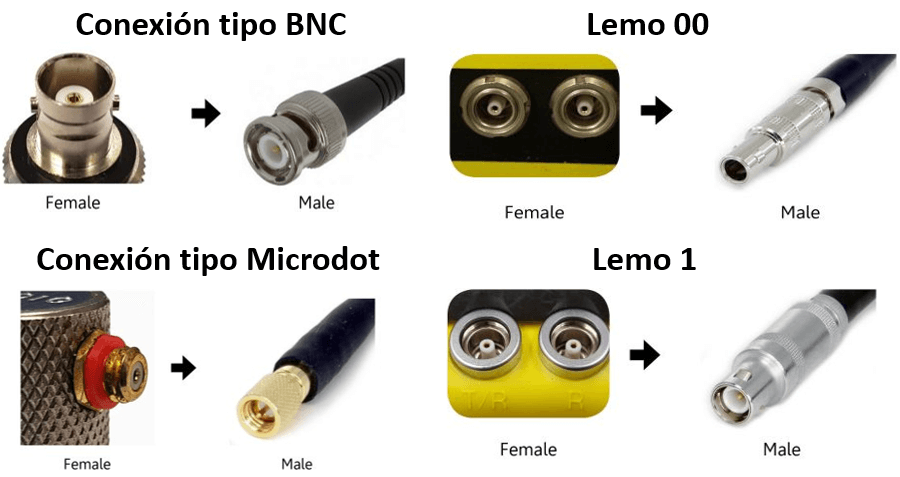
En la figura anterior se observan cuatro tipos de conectores:
- Conexión Tipo BNC.
- Conexión Tipo Microdot.
- Conexión Tipo Lemo 00.
- Conexión Tipo Lemo 1.
Ahora bien, ciertamente existen diversos tipos de conectores, pero el cable como tal solamente se implementa un solo tipo. El cable que se utiliza es el cable coaxial. En la siguiente figura se observa el cable coaxial con las partes que lo conforman.

Tal y como se aprecia en la figura anterior el cable coaxial está conformado por un conductor centra, un aislante, una malla de cobre o aluminio y una cubierta exterior que protege el cable.
5. Acoplante
El acoplante es una necesidad para la elaboración de la inspección ultrasónica. La función del acoplante es excluir la presencia del aire entre el transductor y la pieza evaluada para que la onda ultrasónica pueda propagarse a la pieza a evaluar. En la siguiente figura se aprecia como el acoplante liquido elimina el espacio de aire entre el transductor y la pieza evaluada.

Tal y como se aprecia en la figura 5.1 se observa que el líquido elimina el espacio de aire. Tal y como se explicó en la teoría de propagación sabemos que la onda ultrasónica no tiene la capacidad de propagarse en un medio gaseoso como el aire y es por ello que la presencia del acoplante es crucial.
Los acoplantes a utilizar deben cumplir ciertas consideraciones, a continuación, se presentan algunas características:
- Mojabilidad
La mojabilidad es la capacidad que tienen los líquidos de extenderse por una superficie. Lo que se busca con esta propiedad es que el acoplante tenga una buena capacidad de mojabilidad para que esté presente.
Un ejemplo de mala mojabilidad es en el caso de que agua se ponga sobre una superficie encerada, el agua no mojara la superficie. Lo que se busca es el efecto opuesto.
- Viscosidad
La viscosidad es la capacidad que poseen los fluidos de resistir a las deformaciones. De manera general podemos hablar del espesor que tendría un fluido si se coloca sobre una superficie.
El valor de la viscosidad variara dependiendo de la aplicación a desempeñar, pero de manera general siempre se busca la menor viscosidad ya que el espesor del acoplante será menor y por lo tanto afectara en menor medida los resultados de la inspección.
- No puede generar daños al material a inspeccionar
Es crucial de que el acoplante no genere ningún daño el material a inspeccionar. Hay que mantener la condición de ensayo no destructivo.
Existen listas de materiales permitidos para ser utilizados como acoplantes. Es muy importante saber que se está inspeccionando para no utilizar algún material que pueda repercutir en un daño del mismo.
- Fácil de remover
Esta característica es importante para poder dejar el material evaluado tal cual como se encontró.
- No Corrosivos
El acoplante no se debe reaccionar con el material inspeccionado. Y sobre todo evitarlo con materiales susceptibles a corrosión o agrietamiento. Hay que recordar que el ensayo es no destructivo y no debemos afectar la integridad del componente inspeccionado.
- No Toxico
Se debe procurar que el acoplante sea no toxico para evitar que el personal técnico sufra de intoxicación con el manejo del acoplante.
- Temperatura de la superficie
Es muy importante saber la temperatura de la superficie ya que el acoplante se puede evaporar. Existen acoplantes especializados para su utilización en superficies con temperaturas calientes. Es muy importante acotar que algunos acoplantes poseen elementos nocivos para el ser humano si se encuentran en estado gaseoso, es por ello que es muy importante saber la temperatura de la superficie y si el acoplante es seguro de utilizar.
- Atenuación del Acoplante
Hay que buscar que la atenuación producida por el acoplante sea la mas baja posible para reducir perdidas de la energía de la onda ultrasónica cuando pasa a través del acoplante.
- Impedancia Acústica
Se debe buscar que la impedancia acústica del acoplantes sea similar a la del material inspeccionado. Esto se busca para que la cantidad de energía transmitida al material sea la mayor posible.