Calibración
Sabemos que los ensayos no destructivos son técnicas que se basan en mediciones indirectas de ciertas propiedades.
La calibración básicamente es la configuración del sistema de inspección acorde a ciertos valores de referencia que garantiza que la inspección ofrece resultados reales ya que la calibración compara valores de prueba con medidas conocidas.
Por lo tanto, el proceso de inspección es básicamente la comparación de algo conocido con algo desconocido. Es la comparación del patrón con la pieza inspeccionada.
Ahora bien, el termino calibración podemos decir que por la jerga común se conoce como el termino de ajustar el equipo a los valores adecuado para que el equipo de inspección genere los resultados correctos.
Pero vamos a basarnos en la práctica recomendada SNT-TC-1A y vamos a definir Calibración y Estandarización.
Calibración, Instrumento: La comparación de un instrumento con una referencia, normalmente trazable al Instituto Nacional de Estándares del país aplicable.
Estandarización, Instrumento: el ajuste de un instrumento de NDT usando una referencia apropiada para obtener o establecer una respuesta conocida y reproducible. (Normalmente se ejecuta previo a la examinación, pero puede ser efectuada en cualquier momento que se tenga duda en la respuesta del equipo).
De estas definiciones podemos decir que el termino correcto para lo que coloquialmente decimos como calibración es estandarización.
Si hablamos de calibración nos estamos refiriendo al procedimiento de ajuste y comparación con respecto a una referencia trazable al instituto nacional de estándares que como por ejemplo puede ser la calibración por un laboratorio acreditado bajo la norma ISO/IEC 17025.
1. Parámetros generales a considerar en la estandarización
Aquí solamente mencionaremos algunos parámetros fundamentales que se deben estandarizar para que el equipo de ultrasonido pueda ofrecer resultados reales.
1.1 Velocidad
La velocidad es un parámetro que se debe estandarizar en función del material a inspeccionar. Como ya se ha explicado el equipo basa su calculo en el tiempo de vuelo y la velocidad de la propagación para llevar a cabo los cálculos, por lo tanto, la velocidad es fundamental.
1.2 Sensibilidad
La sensibilidad es la capacidad que posee el sistema ultrasónico de mostrar reflectores de cierto tamaño a una distancia determinada. En otras palabras, establece que tan sensible es el sistema para poder mostrar lo que a través de la detectabilidad puede ver.
La sensibilidad en un sistema ultrasónico depende básicamente de cinco factores:
- Angulo del haz ultrasónico.
- Distancia del campo cercano
- Ancho de banda del transductor
- Material del cristal piezoeléctrico
- Relación señal-ruido del sistema
La estandarización del sistema de inspección dependerá de que norma o criterio de aceptación se esté implementando.
1.3 Resolución
La resolución es la capacidad que posee el sistema de inspección de mostrar de manera individual dos indicaciones muy próximas entre sí. Mientras mejor sea la resolución la proximidad entre las indicaciones podrá ser menor y aun así se podrán mostrar dos indicaciones independientes.
Este factor se estandariza con ciertos bloques de calibración que lo permiten.
1.4 Linealidad Horizontal
La linealidad horizontal hace referencia a que la escala horizontal del instrumento de inspección, la escala de distancia, es proporcional al movimiento físico.
En el proceso de estandarización se ajusta de manera adecuada la linealidad horizontal.
1.5 Linealidad Vertical
La linealidad vertical de la pantalla hace referencia a que las variaciones de la amplitud en el eje vertical de la señal tengan un comportamiento lineal.
En el proceso de estandarización se ajusta de manera adecuada la linealidad vertical.
1.6 Señal relación-ruido
El ruido en las señales ultrasónicas degrada la calidad de la imagen de inspección y por lo tanto aumenta la dificultad de analizar de manera correctas las señales obtenidas.
Esa relación entre la señal y el ruido se conoce como SNR (Signal to Noise Ratio). Normalmente se requiere de una relación SNR de un mínimo de 3:1
El ruido como tal tiene múltiples origines que tienen que ser tomados en cuenta.
En la siguiente figura podemos apreciar el efecto del ruido en una imagen tipo A.
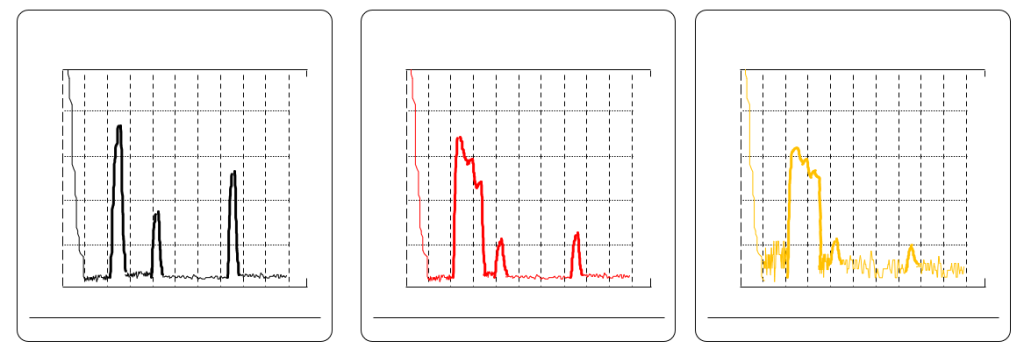
Tal y como se aprecia en la figura anterior, se ve como de izquierda a derecha el nivel de ruido aumenta y dificulta la evaluación de las indicaciones.
A continuación, se listarán algunas de las variables que pueden afectar la SNR:
- El tamaño del transductor y las propiedades focales.
- La frecuencia y ancho de banda.
- El recorrido sonoro y la distancia.
- La interfaz.
- Aspereza de la superficie.
- Ubicación de la indicación con respecto al haz.
- El ruido inherente al material inspeccionado.
- La reflectividad inherente de la indicación.
- Indicaciones multifacéticas tenderán a dispersar la reflexión.
- Tipo de discontinuidad.
- Tamaño de la indicación. Mayor tamaño produce mejor sensibilidad.
- Focalización del haz ultrasónico. Mas focalizado produce mejor sensibilidad.
- La duración del pulso afectara el SNR. Mientras más pequeño el pulso mejor será la detectabilidad.
- El SNR disminuye cuando la densidad del material o la velocidad de la onda aumentan. El SNR es inversamente proporcional a la densidad y a la velocidad acústica.
- El SNR usualmente aumenta con la frecuencia. Pero dependiendo del material puede que el SNR sea independiente de la frecuencia.
2. Bloques de Calibración
Dentro de la industria existe una gran variedad de patrones de calibración que se pueden implementar para equipos de ultrasonido. La selección del patrón dependerá de una serie de factores:
- Aplicación.
- Material a inspeccionar.
- Forma y tamaño de la pieza a inspeccionar.
- Sistema de inspección.
- Norma y/o procedimiento utilizado.
Para las estandarizaciones los bloques de calibración utilizan reflectores que generan las reflexiones con las que se realizan las mediciones y los ajustes necesarios dependiendo del bloque implementado. A continuación, presentaremos una lista de los reflectores utilizados.
2.1 Reflectores
Reflectores esféricos
Este tipo de reflectores son utilizados mayoritariamente en las técnicas ultrasónicas por inmersión ya que la naturaleza del transductor permite una evaluación del campo ultrasónico del transductor.
Debido a la geometría esférica del reflector la energía sonora se dispersa luego del impacto y no regresa al transductor. Esto es debido a que el área efectiva de reflexión es mucho menor si se compara con un reflector plano del mismo diámetro que el reflector esférico.
Los reflectores esféricos pueden ser fabricados de cualquier material, pero comúnmente se fabrican bolas de acero debido a los siguientes factores:
- Acabado superficial muy bueno.
- Se pueden fabricar de tamaños muy pequeños.
- El costo de fabricación es razonablemente bajo.
Reflectores planos (Flat-Bottom Holes)
Los reflectores planos son norma en calibraciones de contacto y de inmersión. Los reflectores son orificios taladrados con fondo plano (realizados con fresadora). El tamaño de estos reflectores dependerá del bloque de calibración o de la norma implementada pero básicamente lo que variaría seria el diámetro del orifico y su profundidad.
Este tipo de reflectores puede perder un alto porcentaje de la reflexión si hay una desviación del ángulo de incidencia. Por lo tanto, la superficie en donde repose el transductor y el proceso de fabricación del transductor es crucial para que el reflector sea aceptable para la calibración.
Muescas
Las muescas son utilizadas para evaluar la capacidad de detección de grietas próximas a la superficie o que incidan en la superficie, como grietas.
Las muescas tienen una sección plana y una cierta profundidad en relación a la superficie del patrón. Usualmente las muescas son perpendiculares a la superficie del patrón, pero dependiendo del proceso de inspección se pueden requerir que tengan un cierto ángulo en relación a la superficie.
Existen varios procesos de fabricación que se pueden implementar para la elaboración de estos reflectores. Como el uso de una fresadora, sierras circulares, maquinado por descarga eléctrica, entre otros.
Reflectores Laterales
- Los SDH son perpendiculares a la superficie de entrada.
- Este tipo de reflectores provee de mucha repetibilidad.
- Se pueden ubicar a cualquier profundidad de la superficie de entrada
- Puede ser utilizado para ondas longitudinales como para ondas transversales.
- Este tipo de reflector se suele utilizar para la calibración de sensibilidad y curva DAC.
2.2 Bloques de Calibración
2.2.1 Bloques de Múltiples Pasos.
Este tipo de bloques de calibración son excelentes para equipos destinados a la medición de espesores ya que la naturaleza de este bloque es representar diferentes espesores de un mismo material.
Generalmente estos bloques son de superficie plana, pero dependiendo de la aplicación y de la norma del bloque se pueden encontrar curvos. En la norma ASTM E-797 (Practica Estándar para la medición del espesor por Ultrasonido Manual Método de contacto pulso-eco) se puede encontrar uno de los estándares para este tipo de bloques. En la siguiente figura se aprecia el croquis que se encuentra en dicha norma:
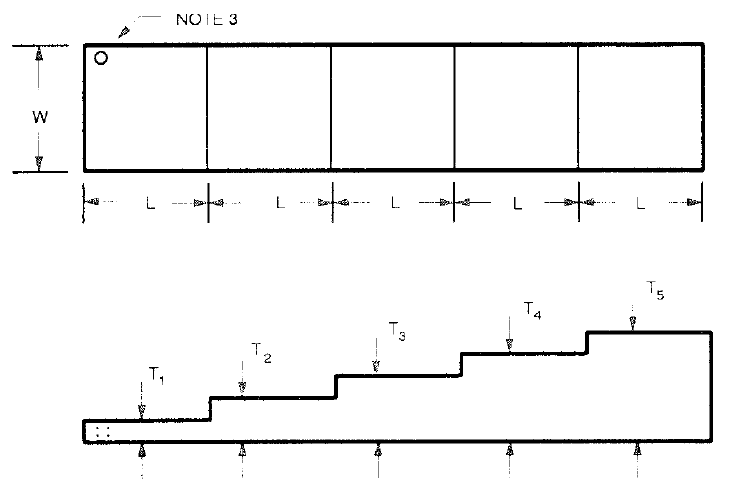
Tal y como se aprecia en la Figura el bloque consiste de varios “pasos” en los cuales cada uno representa un cierto espesor del mismo material.
Este tipo de bloques son especialmente útiles para medición de espesores con transductores duales, ya que sabemos que este tipo de transductor posee un rango mínimo y máximo de penetración de inspección.
2.2.2 Bloques de Distancia/Área Amplitud y Navships
Este tipo de bloques de calibración usualmente se venden en sets de 10 piezas. Básicamente cuentan con un reflector con fondo plano. Estos patrones permiten la medición de la zona muerta, sensibilidad y linealidad de la distancia. En la siguiente figura se aprecia un set de estos bloques:

Tal y como se aprecia en la Figura se aprecia un ser de 10 bloques de aluminio. La norma ASTM E-127 establece la normativa para este tipo de bloques. Por su parte la norma ASTM E-428 establece la normativa para los bloques de acero inoxidable.
Este tipo de bloques son muy buenos para aplicaciones en donde el paso del ultrasonido es lineal ya que la geometría del bloque limita el movimiento. Así que para aplicaciones en donde la aplicación requiera un paso del ultrasonido angular se puede utilizar el bloque conocido como Navship. En la siguiente figura se aprecia dicho patrón:

Tal y como se aprecia en la Figura este bloque posee una geometría que permite que el haz ultrasónico tenga un paso angular. Se observa que el principio es exactamente el mismo que los bloques de Distancia/Área ya que también posee reflectores de fondo plano a diferentes profundidades. La diferencia es que todos se encuentran en el mismo bloque y la geometría varia.
2.2.3 Bloque IIW
Este bloque es uno diseñado, por el Instituto Internacional de Soldadura (IIW por sus siglas en ingles), específicamente para la inspección con haz angular. Este se podría decir que es el bloque principal para todas las aplicaciones de inspección angular.
Con este bloque podemos:
- Localizar el punto de salida del haz.
- Verificar y medir el ángulo de refracción
- Calibrar la velocidad
- Calibrar el retraso de la zapata
- Calibrar la sensibilidad del haz angular
- Calibrar la sensibilidad del haz recto
- Calibración de la resolución
- Verificar la penetración
En la norma ASTM E-164, titulada: “Practicas estándar para la inspección mediante ultrasonido de contacto de cordones de soldadura”, podemos encontrar las especificaciones de los bloques tipo IIW.
A continuación, se detallará cada una de las partes del bloque IIW y sus funciones para el proceso de calibración.
- Cálculo del punto de salida del haz ultrasónico.
El bloque IIW tiene una sección destinada para el cálculo del punto de salida del haz ultrasónico. En la siguiente imagen se puede apreciar el transductor de haz angular en una cierta posición del bloque para dicho calculo.
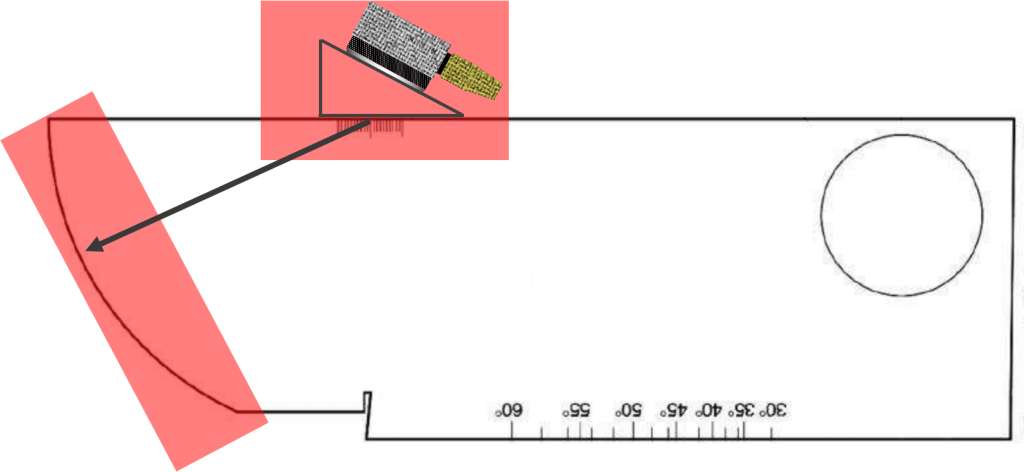
Como se observa en la figura el transductor de haz angular se coloca en la sección plana más larga del perfil del bloque. Las secciones resaltadas en color rojo son las utilizadas para el cálculo del punto de salida en la zapata.
Es evidente que debido a la geometría planteada el haz ultrasónico se moverá hacia la zona curva del bloque IIW (también resaltada de rojo).
Ahora bien, el procedimiento en si consiste en colocar el transductor en la sección definida. En dicha sección se aprecia una regla graduada la cual permitirá definir cuál es el punto exacto. Este valor se obtiene mediante el movimiento lineal del transductor. En la siguiente figura se aprecia el movimiento.

El movimiento del transductor afectara directamente la altura de pantalla del pico en la imagen A-Scan. Lo que se busca es encontrar el punto más alto posible del A-Scan ya que ese será el punto de salida del haz ultrasónico. Una vez se establezca la ubicación del punto de salida se deberá ubicar manualmente sobre la zapata del transductor.
- Verificación y medición del ángulo de refracción
El bloque IIW tiene una sección destinada para la verificación del ángulo de refracción. En la siguiente imagen se puede apreciar el transductor de haz angular en una cierta posición del bloque para dicha verificación.
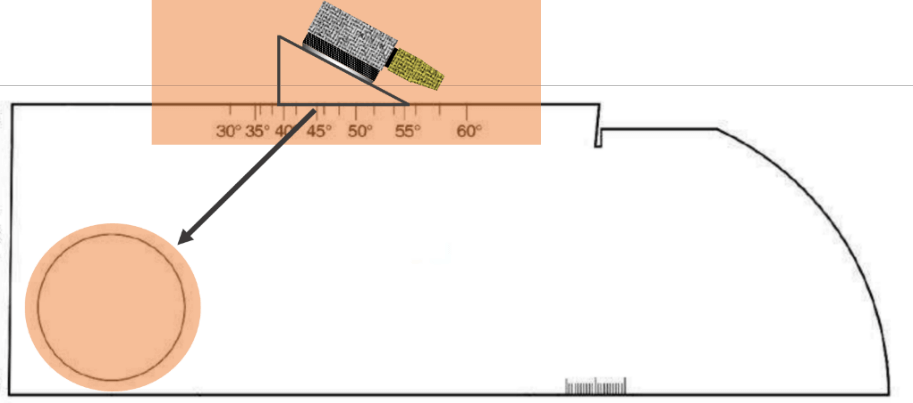
Es importante acotar que esta verificación se debe hacer luego de que el punto de salida del haz ultrasónico haya sido determinado.
La verificación del haz ultrasónico se realiza colocando el transductor tal y como se aprecia en la figura anterior. Luego se deberá mover hacia adelante y hacia atrás y buscar el pico de pantalla es el más alto.
Se seleccionará el ángulo del bloque en función del punto salida que fue marcado en la zapata. El ángulo seleccionado será el que se deberá ingresar en el sistema de inspección. Hay que recordar que existe una tolerancia según la norma que se utilice (normalmente es de 2 grados).
- Calibración de la resolución
El bloque IIW tiene una sección destinada para la calibración de la resolución. El único detalle es que para esta calibración el transductor debe ser de haz recto.
En la siguiente imagen se puede apreciar el transductor de haz recto en una cierta posición del bloque para dicha calibración.
