1. Métodos de Evaluación
Cuando una indicación es hallada por el sistema de inspección ultrasónica normalmente se requiere estimar su tamaño para determinar los resultados de la inspección.
El proceso de análisis y de evaluación de las discontinuidades muchas veces recae en la habilidad y experiencia del técnico, además de contar con un equipo que funcione en optimas condiciones y seguir de manera correcta los procedimientos y normas dispuestos para la evaluación.
De manera general se presentará a continuación una lista de los factores que pueden influir en la correcta evaluación de los resultados de una inspección mediante el método de ultrasonido.
- Exactitud de la calibración.
- Tipo de discontinuidad evaluada.
- Orientación de la discontinuidad.
- Tamaño de la discontinuidad.
- Forma de la discontinuidad.
- Ubicación de la discontinuidad.
- Tipo y condiciones del material inspeccionado.
- Características del transductor.
- Características del haz ultrasónico.
- La experiencia del personal en la reflexión ultrasónica de una discontinuidad en particular.
1.1 Comparación con reflectores de referencia
Tenemos los siguientes puntos a comentar:
- Esta técnica de evaluación es aplicable en inspecciones con transductores de haz recto, haz angular y doble cristal.
- El ajuste de la sensibilidad de la inspección se efectúa contra reflectores de referencia con dimensiones conocidas. Dichos reflectores se encontrarán en los bloques de calibración determinados para dicha inspección.
- Se requiere maximizar la indicación.
- Una manera de efectuar la evaluación puede ser mediante la implementación de la curva de distancia-amplitud, mejor conocida como curva DAC.
- Otra manera que se puede implementar la evaluación es a través de la técnica de la caída de los 6 dB.
- Otro punto que también se puede ocupar en ocasiones es la compensación por diferencia de atenuación entre la pieza y el bloque de inspección.
- Este método de evaluación se puede implementar en uniones soldadas, piezas fundidas, piezas forjadas, etc.
A continuación, detallaremos un poco más algunos de los puntos mencionados anteriormente.
1.1.1 Curva de Distancia Amplitud, curva DAC
Como hemos visto hasta ahora sabemos que a medida que la indicación aumenta su profundidad (distancia con respecto al transductor) su amplitud ira disminuyendo producto de la atenuación.
Debido a esto es necesario recurrir a un método de evaluación que permita saber el comportamiento de la amplitud de una discontinuidad en función de su amplitud y para esto justamente es que se implementa la curva DAC. Tal y como su nombre indica DAC es la abreviación en ingles para curva de corrección de la distancia y la amplitud. Por lo tanto, esta curva permitirá saber cómo se comportará la amplitud de una indicación especifica en función de la profundidad.
Para generar la curva DAC por lo tanto se requiere ocupar un bloque o bloques de calibración que tengan reflectores del mismo tamaño a profundidades diferentes, una manera de realizar esto es con los bloques ASTM tipo “B”.
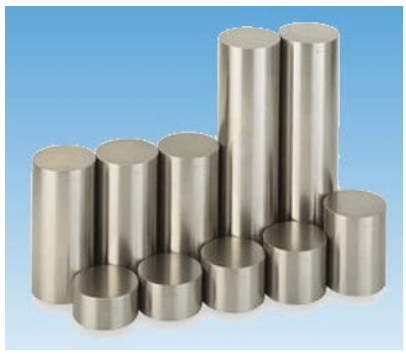
Haciendo uso de estos bloques o de otros bloques indicados se podrá generar la curva DAC. Con fines educativos a continuación se presentará una imagen con un bloque que posee varios reflectores a profundidades diferentes y se verá como se genera la curva DAC.
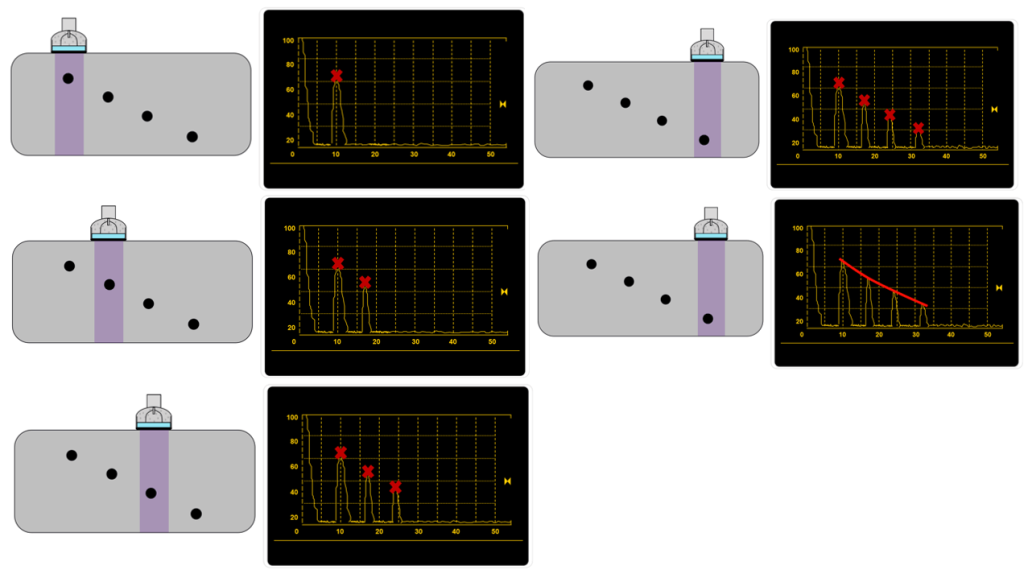
Tal y como se aprecia en la figura anterior cada indicación generara una amplitud diferente a una profundidad diferente. Si se traza una línea con las amplitudes máximas de cada indicación se generará la curva DAC.
De manera general se puede establecer el siguiente procedimiento:
- Maximizar la indicación del reflector.
- Ajustar la indicación a un 80% de altura de pantalla (±5).
- Marcar sobre la pantalla la posición del pico.
- Repetir los pasos anteriores con cada indicación.
- Se traza una línea por los puntos y así se genera la curva DAC.
Evidentemente hoy en día existen equipos que realizan la curva DAC de manera automatizada y no se requiere marcar la pantalla ni hacer el trazo como tal. Pero tradicionalmente se realizaba así hasta la modernización de los equipos de UT.
1.1.2 Técnica de la caída de los 6dB
La técnica de la caída de los 6dB consiste en la caracterización de la longitud de la discontinuidad.
Luego de obtener la máxima amplitud producto de una indicación se procede a desplazar el transductor hasta que debido a la discontinuidad se tenga una caída del 50% de la amplitud con respecto a su amplitud máxima. Si recordamos la relación entre amplitud y decibeles tendremos que la caída del 50% es equivalente a una reducción de 6dB de la amplitud máxima.
En la siguiente figura se ilustra este fenómeno.

Tal y como se aprecia en la figura anterior apreciamos que la parte a de la figura se tiene una amplitud aproximada del 80% de altura de pantalla y al aproximarse al extremo de la discontinuidad la amplitud tiene una reducción del 50% de la señal.
La explicación teórica es muy sencilla y se puede observar en la parte b de la figura anterior. Lo que explica este fenómeno es el hecho de que el 50% de la onda ultrasónica no esta impactando con la indicación y por lo tanto la cantidad de energía sonora que regresa al transductor se ve reducida en un 50%.
Este procedimiento se puede implementar en cualquier dirección y las cantidades que se deseen para permitir que la determinación de la discontinuidad sea la más precisa posible. Evidentemente, lo mejor será seguir el procedimiento de inspección.
Por otra parte, hay ciertas consideraciones que hay que tomar en cuenta a la hora de implementar la caída de los 6dB pero el factor principal es la morfología de la indicación inspeccionada.
1.2 Método de evaluación por caída de amplitud
Este método de evaluación lo podemos definir bajo los siguientes puntos.
- Aplicable en la inspección de piezas con superficies paralelas, usando normalmente haz recto.
- Utilizada para determinar el contorno y extensión de una discontinuidad.
- La calibración en distancia se realiza empleando múltiplos de la reflexión de la pared posterior de la pieza evaluada, tomando una zona sana del material.
- El ajuste de sensibilidad se realiza colocando la primera reflexión de la pared posterior en una amplitud fija entre el 50% y 75% de la escala vertical de la pantalla. Tomando una zona sana de la pieza.
- Se implementará la técnica de la caída de los 6dB.
- Normalmente se implementa en la inspección de placas y piezas forjadas.